How to Choose the Perfect Conveyor Belt for Your Business
Choosing the right conveyor belt for your business is a critical decision that can significantly impact productivity, efficiency, and overall operational costs.
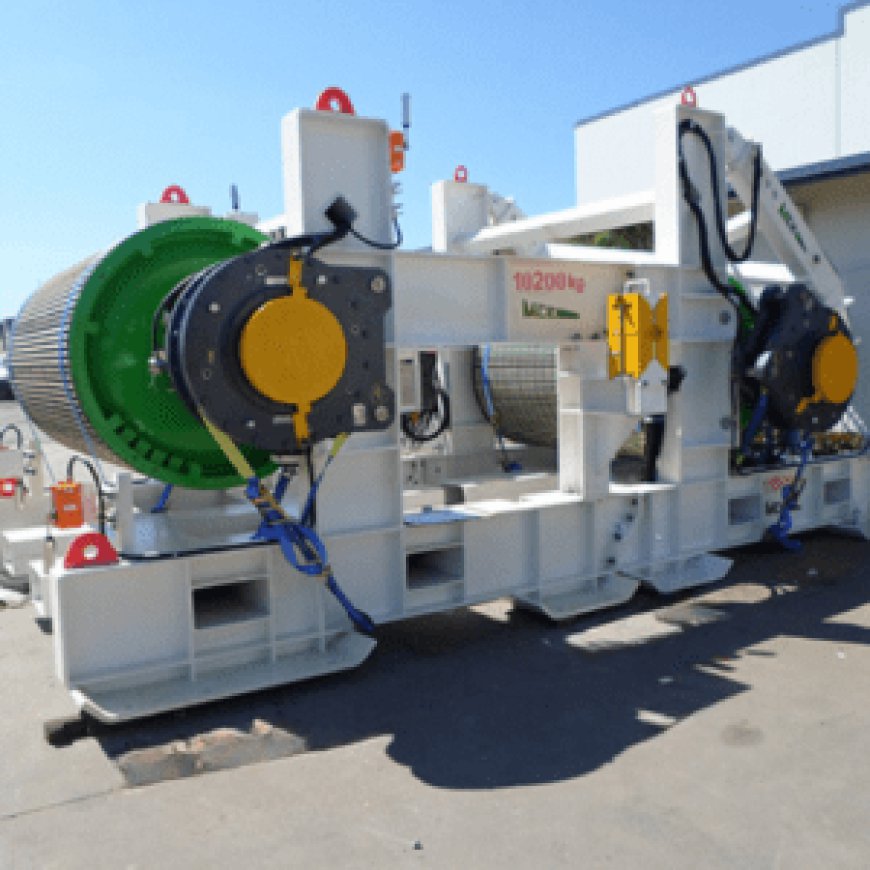
Whether you're running a manufacturing facility, warehouse, or processing plant, the conveyor belt plays a pivotal role in ensuring smooth operations. This guide provides key considerations to help you select the perfect conveyor belt for your specific needs.
1. Understand Your Operational Needs
The first step in choosing the ideal conveyor belt & Pulley lagging is to assess your specific operational requirements. Consider the following questions:
- What type of materials will the conveyor handle?
Identify whether you are transporting heavy, abrasive materials, delicate items, or bulky goods. The type of material directly influences the belt's material and design. - What is the weight and size of the items?
Conveyor belts are designed to handle varying weights and sizes. Ensure the belt can accommodate your product dimensions without overloading or causing inefficiency. - What is the operating environment?
Evaluate the environmental conditions where the conveyor will operate. Factors such as temperature extremes, humidity, or exposure to chemicals will determine the belt's durability requirements.
2. Choose the Right Belt Material
The belt material is crucial to its performance and longevity. Common materials include:
- Rubber: Known for flexibility and durability, rubber belts are suitable for heavy-duty applications and environments with wear and tear.
- PVC or PU: These materials are ideal for food-grade applications and areas requiring resistance to moisture or oil.
- Metal: For high-temperature or abrasive conditions, metal belts offer superior strength and durability.
- Fabric: Lightweight and cost-effective, fabric belts are suitable for smaller loads and low-impact environments.
Each material has unique properties, so align your choice with the specific demands of your operations.
3. Consider the Conveyor Type
The type of conveyor you use will determine the kind of belt required. Common conveyor types include:
- Flat Belt Conveyors: Used for simple transportation of materials in a straight line.
- Modular Belt Conveyors: Designed for flexibility, these belts are easy to maintain and suitable for curved paths.
- Inclined or Declined Conveyors: If your operation involves moving items up or down, choose belts with grip or cleats to prevent slippage.
- Specialty Conveyors: For unique processes such as drying or cooling, belts with perforations or specific coatings may be required.
Match the conveyor type to the nature of your operations for maximum efficiency.
4. Evaluate Load Capacity and Speed
The conveyor belt & Conveyor Trackers must support the load and speed requirements of your operations without compromising performance.
- Load Capacity: Determine the maximum weight the belt will carry. Overloading can lead to belt failure, operational delays, and increased maintenance costs.
- Speed: The conveyor’s speed should match your production rate to avoid bottlenecks or product damage. Adjustable speed settings can provide added flexibility.
Consult with technical experts or refer to load and speed specifications to ensure your belt performs efficiently.
5. Prioritize Durability and Maintenance
A durable conveyor belt can withstand wear and tear, reducing downtime and replacement costs. Look for belts with robust construction and resistance to factors such as:
- Abrasion
- Chemical exposure
- Temperature fluctuations
- Moisture and humidity
Additionally, consider ease of maintenance. Belts designed for quick replacement or minimal upkeep save time and reduce operational disruptions.
6. Ensure Compliance with Industry Standards
If your business operates in regulated industries, such as food processing or pharmaceuticals, ensure the conveyor belt meets relevant safety and hygiene standards. Look for certifications that guarantee compliance with industry-specific requirements. For example:
- Food-grade belts: Should be non-toxic, easy to clean, and resistant to bacteria.
- Heat-resistant belts: Required for high-temperature operations like baking or metalwork.
Compliance not only ensures safety but also prevents potential legal issues or product recalls.
7. Plan for Scalability
Choose a conveyor belt that can adapt to future growth or changes in operations. Scalability ensures you won't need a complete overhaul when production demands increase. Modular belts or customizable designs can be excellent options for expanding operations.
8. Factor in Cost-Effectiveness
While it’s tempting to opt for the cheapest option, consider the total cost of ownership. A low-cost belt may incur higher maintenance and replacement expenses over time. Balance initial investment with long-term benefits, including durability, energy efficiency, and reduced downtime.
9. Test Before Purchase
Whenever possible, test the conveyor belt in real-world conditions before making a purchase. Testing helps you verify compatibility with your systems, material handling capabilities, and overall performance.
10. Consult Industry Experts
If you’re unsure about specific requirements, consult industry experts or suppliers. They can provide tailored recommendations based on your unique needs and operational environment. Working with knowledgeable professionals ensures you select a conveyor belt optimized for performance and longevity.
Conclusion
Selecting the perfect conveyor belt for your business involves careful evaluation of operational needs, material specifications, and environmental factors. By understanding these elements and prioritizing durability, compliance, and cost-effectiveness, you can invest in a solution that enhances productivity and minimizes downtime. Take the time to research and consult with experts to make an informed decision that supports your long-term goals.
Read Also: Durable Rubber Screen Panels