Key Trends for Cement Production Companies: Navigating Innovation and Sustainability in 2024-2025
Key Trends for Cement Production Companies: Navigating Innovation and Sustainability in 2024-2025
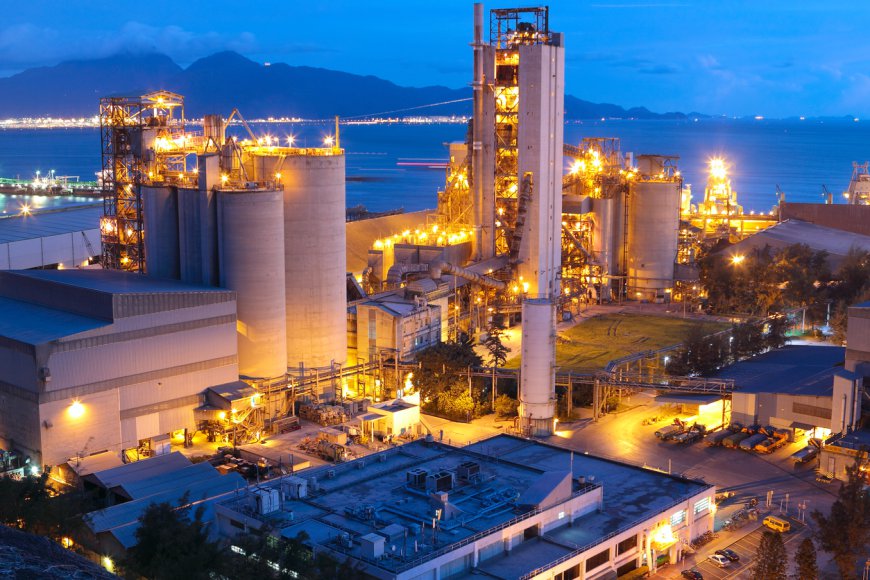
As we look ahead to 2024-2025, the cement production industry is poised for major changes driven by sustainability initiatives, digital transformation, and evolving market demands. Cement production companies need to stay ahead of these trends to remain competitive, cost-effective, and environmentally responsible. This post highlights the most important trends and strategies cement manufacturers should adopt to thrive in the next few years.
Sustainability as a Core Focus: Building for a Greener Future
Sustainability is at the heart of the cement industry's future. Cement production is one of the largest sources of CO2 emissions globally, making it crucial for manufacturers to adopt greener practices.
Key Sustainable Practices for Cement Production Companies:
- Alternative Fuels: Transitioning from fossil fuels to renewable or alternative fuels, such as biomass, waste-derived fuels, and industrial by-products.
- Low-Carbon Cements: Using innovative materials such as fly ash, slag, and limestone calcined clay to reduce clinker content and emissions.
- Carbon Capture and Storage (CCS): Implementing CCS technologies to capture and store CO2 emissions, minimizing environmental impact.
- Circular Economy: Incorporating recycled materials such as construction debris, plastics, and rubber to reduce raw material usage and waste.
Digitalization and Automation: Transforming Cement Production Operations
The digital revolution is transforming every industry, and cement production is no exception. Automation and digital technologies are enabling cement companies to operate more efficiently, reduce costs, and enhance product quality.
How Automation and Digitalization Benefit Cement Manufacturers:
- AI and IoT Integration: Using AI and IoT technologies to monitor plant operations in real-time, optimize energy consumption, and predict maintenance needs.
- Data-Driven Insights: Leveraging big data and machine learning to gain actionable insights into production processes, improve decision-making, and reduce downtime.
- Digital Twins: Virtual models of cement plants that help manufacturers simulate operations, test scenarios, and identify inefficiencies before implementing physical changes.
Energy Efficiency: Reducing Costs and Environmental Impact
Energy consumption is a significant cost factor in cement production. As energy prices continue to rise and environmental regulations tighten, energy efficiency is more important than ever.
Key Strategies for Improving Energy Efficiency:
- Waste Heat Recovery Systems: Capturing excess heat from the cement production process and converting it into electricity, reducing reliance on external energy sources.
- Renewable Energy Integration: Investing in renewable energy solutions such as solar, wind, or geothermal to power cement production operations and reduce carbon footprints.
- Energy Monitoring Systems: Using advanced energy monitoring systems to track energy usage, identify inefficiencies, and make real-time adjustments to reduce consumption.
Modular and Flexible Plant Designs: Scaling with Market Demands
As the global construction market continues to grow, cement production companies need to be able to scale their operations quickly and efficiently. Modular and flexible plant designs offer a solution to these challenges.
Advantages of Modular and Flexible Cement Plants:
- Faster Construction: Modular plants are pre-engineered and can be quickly assembled, reducing construction time and costs.
- Scalability: Modular plants can be easily expanded or reconfigured to meet changing market demands and increase production capacity.
- Flexibility: Flexible designs allow cement plants to adapt to new technologies, environmental regulations, and production requirements without major overhauls.
Circular Economy: Harnessing Recycled Materials for Sustainable Cement Production
The circular economy is a growing trend, and cement production companies are uniquely positioned to benefit from it by incorporating recycled materials into their processes.
Key Benefits of Embracing the Circular Economy:
- Material Cost Reduction: Using recycled materials such as fly ash, slag, and recycled concrete as substitutes for virgin raw materials can reduce material costs.
- Waste Reduction: Recycling waste from other industries (e.g., construction debris, rubber, plastics) reduces landfill use and helps close the loop in the production process.
- Enhanced Product Quality: Incorporating recycled materials can result in high-quality cement products that meet or exceed the performance standards of traditional cements.
Automation in Quality Control: Ensuring Consistency and Product Excellence
As cement production companies face growing demand for high-quality products, ensuring consistency and quality across every batch is essential.
How Automation Enhances Quality Control:
- Real-Time Monitoring: Automated systems can track the quality of raw materials, production processes, and finished products, ensuring consistency in the final output.
- Predictive Quality Control: Machine learning algorithms can predict potential quality issues before they arise, allowing for timely interventions.
- Reduction in Human Error: Automation reduces the reliance on manual labor for quality control, minimizing the risk of human error and improving overall product reliability.
Green Building Materials and the Rise of Eco-Conscious Construction
The demand for green building materials is growing, driven by a desire for environmentally responsible construction practices. Cement production companies need to tap into this trend by producing eco-friendly cement and partnering with green builders.
How Cement Manufacturers Can Capitalize on the Green Building Trend:
- Eco-Friendly Cement Options: Offer low-carbon cement products that align with the growing demand for sustainable construction materials.
- Certification Programs: Pursue green certifications like LEED (Leadership in Energy and Environmental Design) for your cement products to demonstrate commitment to sustainability.
- Collaborations with Green Builders: Partner with construction firms that specialize in eco-conscious projects to supply cement that meets their sustainability requirements.
Regulatory Compliance and the Importance of Adaptability
Cement production companies face ever-tightening regulations related to environmental protection, emissions standards, and workplace safety. Being adaptable and proactive in meeting these regulations is essential for staying competitive.
Strategies for Regulatory Compliance:
- Stay Informed: Regularly update your knowledge of local and international regulations regarding emissions, waste management, and energy usage.
- Invest in Compliance Technologies: Implement technologies that monitor compliance in real time, helping to ensure that your plant operates within regulatory limits.
- Adapt to Changing Standards: Design plants with the flexibility to adapt to new regulations, such as lower carbon emissions or stricter waste management guidelines.
Conclusion: Leading the Way in 2024-2025
Cement plant manufacturers are facing a rapidly evolving industry where sustainability, automation, and energy efficiency are becoming central to success. As cement production continues to grow in demand, manufacturers must adopt these emerging trends to stay competitive. By focusing on greener production processes, innovative technologies, and cost-saving measures, cement plant manufacturers will be able to improve their operational efficiency and reduce their environmental impact.
To remain ahead of the curve, cement plant manufacturers must continuously innovate and adapt to the latest industry changes. Companies that prioritize sustainability, efficiency, and flexibility will thrive in the coming years.
For more insights on these trends and how to stay ahead in the cement production industry, you can read our blog on the https://www.nntcement.com/blog/trends-in-construction-industry/