The Role and Advancements of Electron Beam Melting in Modern Manufacturing
The Role and Advancements of Electron Beam Melting in Modern Manufacturing
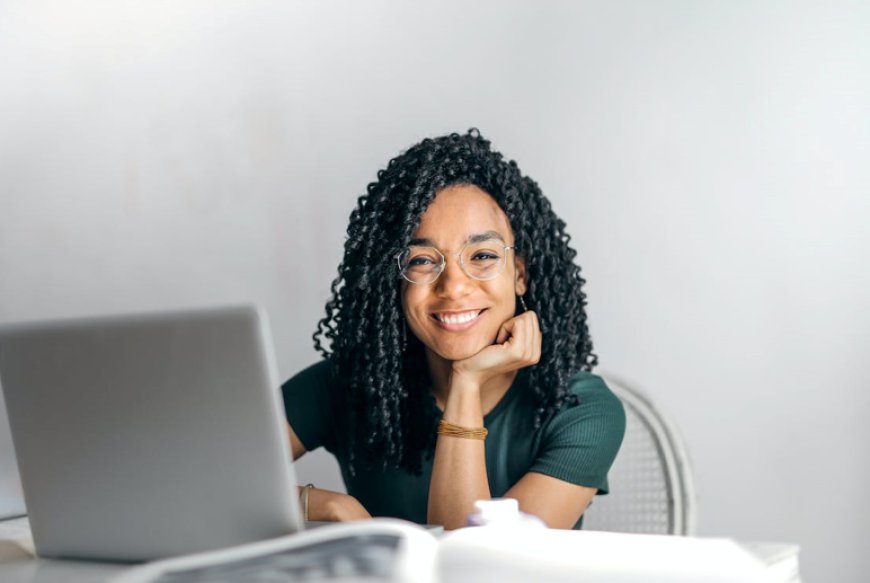
Introduction
Electron Beam Melting machine (EBM) has rapidly evolved as a leading-edge technology in the realm of additive manufacturing, or 3D printing, especially for creating intricate, high-performance metal components. By using a focused beam of electrons to selectively melt metal powder in a layer-by-layer process, EBM is making strides in industries where precision, strength, and complex geometries are critical. Today, EBM’s applications span aerospace, medical, automotive, and energy sectors, where it has enabled the production of innovative parts that were previously impossible to achieve through traditional manufacturing.
How Electron Beam Melting Works
EBM technology stands out for its unique process and capabilities, which include:
- Powder Bed Fusion: EBM begins with a bed of fine metal powder, typically titanium or nickel-based alloys. This powder is distributed evenly across a build platform.
- Electron Beam Control: The machine’s electron gun generates a highly focused beam of electrons, which is directed by magnetic coils to precisely scan and melt designated areas of the powder bed. This follows a CAD model, creating the intricate geometry of each layer.
- Layer Solidification: As the electron beam scans and melts the powder, the molten material quickly solidifies and bonds with the previously melted layer, gradually building up a fully dense, solid structure.
- Vacuum Environment: The entire EBM process takes place in a vacuum chamber, which is necessary to prevent oxidation and ensure the quality of reactive metals like titanium.
EBM’s vacuum environment and the ability to work with high-energy electrons allow it to process high-performance metals in ways that traditional methods struggle to replicate.
Key Advantages of Electron Beam Melting
- Complex Geometries and Design Freedom: EBM allows for the production of parts with internal channels, lattice structures, and complex contours that would be unfeasible with traditional machining.
- High Density and Material Properties: The layer-by-layer melting and solidification process produces parts with high density and strength, making them suitable for demanding applications.
- High Build Speeds for Large Components: EBM’s capability to melt large areas in each pass means it can produce larger parts more quickly than laser-based additive manufacturing systems, especially when working with challenging alloys.
- Reduced Material Waste: Because EBM is an additive process, it uses only the material required to build each part, and any unused powder can often be reused in future builds.
- Customizable Porosity: In applications such as medical implants, EBM can create controlled porous structures that facilitate bone ingrowth, improving the implant’s integration with natural bone.
Applications of Electron Beam Melting Across Industries
- Aerospace: EBM has been transformative for the aerospace industry, enabling the creation of lightweight components with high strength-to-weight ratios. It allows engineers to design intricate structures that reduce weight and improve fuel efficiency.
- Medical Devices: EBM technology is widely used in producing custom orthopedic implants, especially those that benefit from titanium’s biocompatibility and the ability to create complex lattice structures. This technology enables the creation of highly personalized implants that enhance patient outcomes.
- Automotive: The automotive sector uses EBM to produce complex, lightweight parts such as turbochargers, engine brackets, and exhaust components that contribute to vehicle efficiency and performance.
- Energy and Defense: EBM’s ability to process high-performance alloys, such as those resistant to high temperatures and corrosion, makes it ideal for energy and defense applications, where durability and precision are critical.
Challenges and Limitations of EBM Technology
While EBM offers many benefits, it also comes with some limitations:
- High Initial Investment: The cost of acquiring and operating EBM equipment is high, which can make it less accessible for smaller organizations or for lower-volume applications.
- Surface Finish: Parts produced by EBM typically have a rougher surface finish than those produced by other methods, often requiring post-processing for applications where a smoother finish is necessary.
- Material Limitations: While EBM works well with a variety of metals, it is limited to conductive materials and is not suitable for polymers, ceramics, or highly reflective metals.
- Process Complexity: The requirement of a vacuum chamber and the specialized expertise needed for beam control and powder handling increase the operational complexity.
Recent Advancements in EBM Technology
Recent developments in EBM technology have focused on improving machine performance, software integration, and process efficiency. Key advancements include:
- Enhanced Electron Beam Control: Newer EBM systems come equipped with better magnetic beam deflection systems, allowing for greater accuracy and faster build speeds.
- Automated Powder Handling: Advances in powder management have streamlined the powder handling process, reducing operator involvement and increasing safety.
- Real-Time Process Monitoring: New EBM machines are equipped with sensors and cameras that provide real-time feedback, allowing operators to adjust parameters on the fly to ensure part quality.
- AI and Machine Learning Integration: AI and machine learning are being used to analyze data from previous builds, helping optimize process parameters and reduce defects.
The Future of Electron Beam Melting
The future of EBM technology is promising, with ongoing research focusing on expanding its material range, improving build speeds, and lowering costs. The technology is also expected to see broader adoption in new fields, as engineers continue to explore its capabilities in producing lightweight, durable components. Furthermore, with the rise of Industry 4.0 and the demand for smart manufacturing, EBM’s integration with digital production systems and automation tools could make it a key player in next-generation manufacturing.
Conclusion
Electron beam melting machines represent a significant advancement in the world of additive manufacturing, enabling engineers to design and produce complex, high-performance metal parts that were once impossible to achieve. With its unique advantages and expanding applications, EBM is not only pushing the boundaries of design and functionality but also paving the way for more efficient, sustainable manufacturing practices. As technology improves and costs decrease, EBM is poised to become an integral part of modern production, revolutionizing industries and enabling the creation of next-generation products.