The Ultimate Guide to CO2 Hose: Essential Insights and Applications
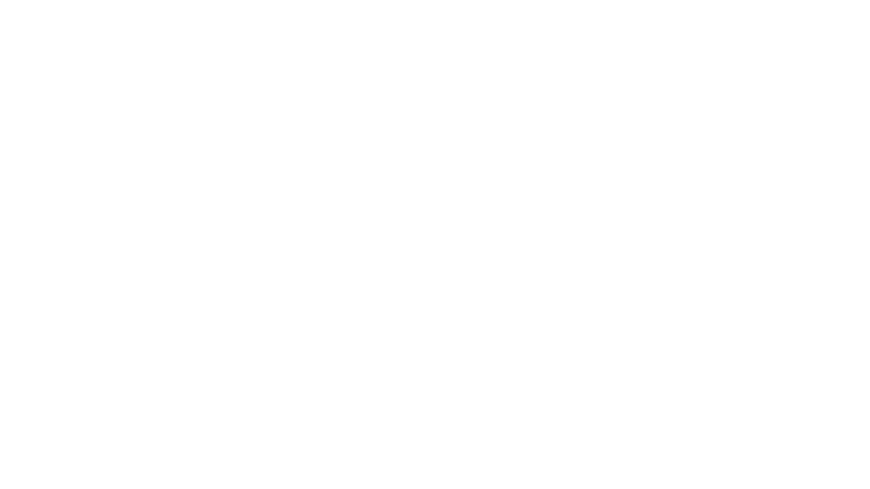
When it comes to handling gases, especially carbon dioxide (CO2), a reliable CO2 hose is paramount. Whether for beverage dispensing, welding, or industrial applications, selecting the right CO2 hose ensures safety and efficiency. In this article, we will explore the various aspects of CO2 hoses, their construction, applications, maintenance, and safety protocols, providing you with comprehensive insights to help you make informed decisions.
Understanding CO2 Hoses: What You Need to Know
CO2 hoses are specialized tubes designed to transport carbon dioxide safely and efficiently from one point to another. They are commonly used in diverse applications, including:
-
Beverage Dispensing: Ensuring consistent pressure for carbonated drinks.
-
Welding: Used in gas-shielded welding processes.
-
Industrial Uses: Employed in various manufacturing processes.
Key Characteristics of CO2 Hoses
-
Material Composition: Most CO2 hoses are made from rubber or thermoplastic materials that can withstand high pressure and resist the corrosive effects of CO2.
-
Pressure Rating: A reliable CO2 hose should have a pressure rating that meets or exceeds the requirements of your application. Typical ratings range from 300 psi to 500 psi.
-
Temperature Tolerance: CO2 hoses should also be resistant to extreme temperatures, ensuring performance in both cold and hot environments.
-
Diameter Options: The internal diameter of the hose affects the flow rate. A larger diameter can deliver more gas but may not be suitable for all applications.
Applications of CO2 Hoses
Beverage Dispensing Systems
In the beverage industry, CO2 hoses play a crucial role in maintaining the carbonation levels of drinks. These hoses connect CO2 tanks to the draft systems, ensuring that the beverage maintains its fizz.
Key Considerations:
-
Compatibility: Ensure the hose is compatible with both the CO2 tank and the beverage dispensing system.
-
Length: The length of the hose can impact the pressure drop; longer hoses may require larger diameters or higher pressure ratings.
Welding Applications
In welding, CO2 hoses are essential for delivering shielding gas to protect the weld pool from oxidation. The correct hose selection can greatly influence the quality of the weld.
Factors to Consider:
-
Hose Flexibility: A more flexible hose allows for easier maneuverability in tight spaces.
-
Durability: Hoses must withstand high temperatures and potential abrasion during welding operations.
Industrial and Manufacturing Uses
In various industrial processes, CO2 hoses are utilized for conveying gases in applications like food processing, refrigeration, and chemical manufacturing.
Important Attributes:
-
Chemical Resistance: The hose should be resistant to chemicals it may encounter in these environments.
-
Reinforcement: Some applications require hoses that are reinforced to handle high pressures without risk of bursting.
Choosing the Right CO2 Hose
Selecting the appropriate CO2 hose involves several critical considerations:
1. Identify Your Application Needs
Understanding your specific application is the first step. Different applications have unique requirements regarding pressure, temperature, and hose length.
2. Assess Material Requirements
Choose a hose material based on its intended use. For high-pressure applications, select hoses made from durable rubber or thermoplastic compounds.
3. Check Certifications
Ensure that the hose complies with industry standards and certifications. This guarantees that the hose is safe for use in your intended application.
4. Evaluate Cost vs. Quality
While it may be tempting to opt for the cheapest option, investing in a high-quality CO2 hose can prevent costly failures and safety hazards down the line.
Maintenance Tips for CO2 Hoses
Proper maintenance can significantly extend the lifespan of CO2 hoses and enhance their performance. Here are some essential tips:
Regular Inspections
Conduct routine inspections to check for signs of wear, such as cracks, fraying, or discoloration. Address any issues immediately to prevent failures.
Cleaning Procedures
Regularly clean the exterior of the hose to remove contaminants. Avoid using harsh chemicals that could damage the hose material.
Storage Conditions
Store CO2 hoses in a cool, dry place, away from direct sunlight and extreme temperatures. Proper storage prevents premature degradation.
Replace When Necessary
If a hose shows significant wear or damage, it’s crucial to replace it immediately. Never attempt to repair a hose that is compromised, as this can pose serious safety risks.
Safety Protocols When Using CO2 Hoses
Safety should always be a priority when working with CO2 hoses. Here are key protocols to follow:
Proper Connection Techniques
Ensure that all connections are tight and leak-free. Use appropriate fittings designed for CO2 hoses to avoid accidental disconnections.
Monitoring Pressure Levels
Regularly monitor the pressure levels within the hose. Sudden pressure changes can indicate potential leaks or blockages.
Emergency Procedures
Familiarize yourself with emergency procedures in the event of a CO2 leak. Know how to shut off the supply and evacuate the area if necessary.
Conclusion: The Importance of a Reliable CO2 Hose
In conclusion, a high-quality CO2 hose is essential for safety and efficiency in various applications, from beverage dispensing to industrial processes. By understanding the characteristics, applications, and maintenance requirements of CO2 hoses, we can ensure optimal performance and longevity. Investing in a reliable CO2 hose not only enhances operational efficiency but also guarantees safety, making it a critical component in any industry utilizing carbon dioxide.