A Comprehensive Guide to the Injectable Manufacturing Process in Pharmaceuticals
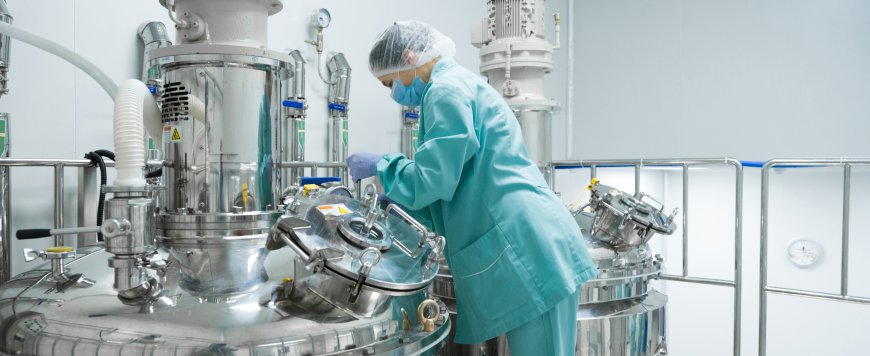
The pharmaceutical industry plays a crucial role in healthcare by developing and producing medications that prevent, treat, and manage a wide range of diseases and medical conditions. One of the most critical areas within this industry is the injectable manufacturing process in pharmaceuticals. Injectable medications, due to their rapid action and high bioavailability, are indispensable in modern medicine, especially in hospitals and emergency care.
In this comprehensive guide, we’ll explore the various stages involved in the injectable manufacturing process, the significance of maintaining sterility, the equipment used, and the key challenges faced by manufacturers. Whether you are a pharmaceutical professional or simply curious about the injectable production process, this article will provide you with valuable insights into how these life-saving drugs are produced.
What is the Injectable Manufacturing Process in Pharmaceuticals?
The injectable manufacturing process in pharmaceuticals refers to the series of steps involved in the production of sterile injectable medications. Injectables are drugs that are administered directly into the body via injections, including intravenous (IV), intramuscular (IM), and subcutaneous (SC) routes. These medications bypass the digestive system, which makes them fast-acting and highly effective for conditions that require immediate intervention.
Due to the nature of their administration, injectable drugs must be manufactured under strict sterile conditions to prevent contamination and ensure patient safety. The process involves several stages, from formulation and preparation to filling, sealing, and packaging, all while adhering to Good Manufacturing Practices (GMP) and regulatory guidelines.
Why Injectables Are Important in Pharmaceuticals
Injectable drugs are an essential category of medications, particularly in critical care. They are widely used in hospital settings and are often administered for the following reasons:
-
Rapid Onset of Action: Injectables deliver medication directly into the bloodstream or muscle tissue, leading to a faster therapeutic effect compared to oral medications.
-
High Bioavailability: Since injectables bypass the digestive system, they have higher bioavailability, meaning the body absorbs a larger percentage of the active ingredient.
-
Targeted Delivery: Injectables can be designed for specific organs or tissues, making them ideal for targeted therapies such as chemotherapy or vaccines.
-
Controlled Dosage: Injectables allow for precise control over the dosage, which is particularly important in critical care or when administering potent drugs.
The precision and sterility of the injectable manufacturing process in pharmaceuticals are therefore paramount to producing safe and effective medications that meet the needs of healthcare providers and patients.
Key Steps in the Injectable Manufacturing Process in Pharmaceuticals
The injectable manufacturing process is a complex and highly regulated procedure that involves several critical stages to ensure the sterility, efficacy, and safety of the final product. Below are the key steps involved in the production of injectable drugs:
1. Formulation Development
The first step in the manufacturing process is the formulation of the injectable drug. This involves creating a solution, suspension, or emulsion that contains the active pharmaceutical ingredient (API) along with other excipients like stabilizers, preservatives, and solubilizers. The formulation must be compatible with the intended route of administration (IV, IM, SC) and stable throughout the shelf life of the product.
Key considerations during formulation include:
-
pH levels: Ensuring that the pH is compatible with the body to avoid irritation or reactions.
-
Tonicity: Adjusting the formulation to match the tonicity of bodily fluids to avoid discomfort or tissue damage upon injection.
-
Stability: Ensuring that the active ingredient remains stable without degrading over time or under different storage conditions.
2. Sterilization of Components
Sterility is one of the most important aspects of injectable manufacturing. To ensure that the product is free from microbial contamination, all equipment, containers, and materials that come in contact with the product must be sterilized. This includes vials, stoppers, and even the air in the production environment.
Common sterilization methods used in the injectable manufacturing process in pharmaceuticals include:
-
Autoclaving: Sterilizing equipment and containers with high-pressure steam.
-
Dry Heat Sterilization: Used for materials that can withstand high temperatures without degrading.
-
Filtration: Sterilizing liquids by passing them through a sterile filter to remove microbes.
-
Gas Sterilization: Using ethylene oxide or other gases for materials that cannot withstand high heat.
3. Aseptic Filling
Aseptic filling is one of the most critical stages in the injectable manufacturing process, as this is when the sterile product is filled into its final container, such as a vial, ampoule, or prefilled syringe. The filling process must be conducted in a controlled environment, such as a cleanroom, to maintain sterility. Advanced technologies like robotic filling systems are often used to reduce the risk of contamination.
Key factors in aseptic filling include:
-
Environmental Control: The filling area must be equipped with HEPA filters to ensure that the air is free from contaminants.
-
Automation: Automated filling lines are used to minimize human contact and the potential for contamination.
-
Precision: Accurate measurement of the drug volume is crucial to ensure consistent dosing in every container.
4. Sealing and Capping
Once the drug has been aseptically filled into its container, the container must be sealed to maintain sterility. For vials and ampoules, this typically involves crimping a sterile rubber stopper or sealing with glass. Prefilled syringes may require capping with a needle guard or other protective mechanisms.
Proper sealing is essential to prevent the entry of contaminants and ensure that the drug remains sterile until it is administered to the patient.
5. Lyophilization (Freeze-Drying) – Optional
For certain injectable products, particularly biologics and vaccines, lyophilization (freeze-drying) may be necessary to extend the product's shelf life. This process involves freezing the product and then removing the water content through sublimation, leaving behind a stable, dry powder. The lyophilized product can then be reconstituted with a sterile solution before administration.
Lyophilization helps maintain the stability of sensitive molecules and enhances the long-term storage of injectable drugs, especially those that are prone to degradation in liquid form.
6. Inspection and Quality Control
Before the product is released for distribution, it must undergo rigorous inspection and quality control testing to ensure that it meets the necessary safety and efficacy standards. This includes:
-
Visual Inspection: Every container is inspected for defects such as cracks, leaks, or particulate matter.
-
Sterility Testing: Samples are taken to ensure that the product is free from microbial contamination.
-
Potency and Purity Testing: Analytical tests are performed to confirm that the active ingredient is present at the correct concentration and that there are no impurities.
Quality control is a critical step in the injectable manufacturing process in pharmaceuticals, as it ensures that the final product is safe, effective, and compliant with regulatory standards.
7. Packaging and Labeling
Once the product has passed quality control, it is ready to be packaged and labeled for distribution. Packaging must ensure the integrity of the product during storage and transport, while labeling must comply with regulatory requirements, including information about dosage, administration, and expiration date.
Packaging options include:
-
Vials and Ampoules: Sealed glass containers for liquid or lyophilized injectables.
-
Prefilled Syringes: Ready-to-use syringes that simplify administration.
-
Cartridges: For use in auto-injectors or other delivery devices.
Equipment Used in Injectable Manufacturing
The injectable manufacturing process in pharmaceuticals relies on specialized equipment to ensure the sterility and precision of the production process. Some of the key equipment includes:
-
Sterile Fillers: Automated machines that fill containers with the sterile drug solution.
-
Autoclaves: Devices used for steam sterilization of equipment and components.
-
Freeze-Dryers: Machines used for lyophilization to remove water from sensitive drugs.
-
Capping Machines: Equipment that seals vials, ampoules, and syringes to maintain sterility.
-
Cleanroom Technology: Controlled environments with filtered air to prevent contamination.
At Laxmi Pharma Equipment, we specialize in providing state-of-the-art equipment that ensures the smooth and sterile operation of the injectable manufacturing process. Our machines are designed to meet the highest standards of GMP and regulatory compliance, ensuring that pharmaceutical manufacturers can produce safe and effective injectable drugs.
Challenges in Injectable Manufacturing
Despite advancements in technology, the injectable manufacturing process in pharmaceuticals presents several challenges, including:
-
Maintaining Sterility: Ensuring that the product remains sterile throughout the production process is a constant challenge that requires strict environmental controls and advanced equipment.
-
Handling Biologics: Injectable biologics, such as vaccines and antibodies, are highly sensitive and prone to degradation, making their production particularly challenging.
-
Regulatory Compliance: Pharmaceutical manufacturers must adhere to strict regulatory guidelines set by agencies such as the FDA, EMA, and WHO. Compliance involves extensive documentation, testing, and validation.
-
Cost Management: The complexity of the manufacturing process, coupled with the need for specialized equipment and cleanroom facilities, can drive up production costs.
Conclusion
The injectable manufacturing process in pharmaceuticals is a complex, highly regulated procedure that ensures the production of safe, sterile, and effective injectable medications. From formulation development to aseptic filling and quality control, each step plays a crucial role in delivering high-quality drugs to patients in need.
At Laxmi Pharma Equipment, we are committed to supporting pharmaceutical manufacturers by providing top-of-the-line equipment designed for the precise and sterile production of injectables. Our machines are built to meet the demands of modern pharmaceutical manufacturing, ensuring that your products are produced to the highest standards.
If you’re looking to optimize your injectable manufacturing process or upgrade your equipment, visit our website at www.laxmipharmaequipments.com for more information on how we can help streamline your production.