A Deep Dive into Injection Molding and the Injection Molding Process
In general injection molding is one of the widely used distribution processes that entails injecting the material in a molten form into a mold in creating parts and products of specific shapes. the injection molding is very efficient and suitable for use in mass production of similar products and is highly used in automotive, consumer, electronics et.c This process is most preferred for making parts with thin sections and complicated geometrical shapes or those which are large since it offers great accuracy and repeatability.
What is Injection Molding?
Injection molding in its primary form is a process by which the plastics or the material which is to be utilised is injected with the aid of a mold. It is through this that mold cools the given material and solidifies in mold in order to achieve the required shape. Another advantage that the injection molding has is the fact that the geometry that is achieved is rather complex and it is easier to achieve using the method in question when the cycle time is shorter.
Injection molding allows production of all kinds of parts and products ranges from electronics, phones, household just to name but a few to automobile parts and major automotive structures. One of which is that the process is very suitable for scaled up, in the sense that prototype production as well as full scale production can be done in this same setup with only slight adjustment. This makes injecting molding especially ideal for use by companies that require high volume production with emphasis on quality.
The Injection Molding Process
The injection molding process has several procedural steps that are indispensable for getting high quality parts. These stages include:
- clamping: The two halves of the mold are closed closer by clamp and it is there and then position to receiver the material.
- Injection: It’s a stage where the molten material is put into the mold cavity where it is subjected to pressure. This is hence the genesis of the injection molding name.
- Cooling: The molten mate-rial is poured into the mould and on solidification gives the required shape of the object to be produced. With regard to the process, cooling is one of the most important factors that affect the quality of a particular product.
- Ejection: Once the part has cooled it is time for the mold to open and the part to be ejected that marks the end of injection molding.
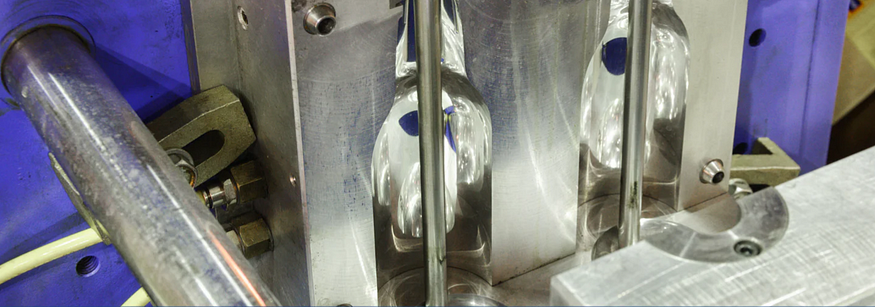
The cycle time of injection moulding is very short and each cycle can be repeated many times and thus thousands or even millions of identical parts can be produced.
Advantages of Injection Molding
Injection molding could be regarded as one of the most popular methods due to one of its main edges: effectiveness. The process is characterized with low waste, high repeatability and it consumes less time hence minimizing the labor cost especially when a large number of products are being manufactured. The injection molding process is also highly achievable in that it can work with varying types of materials such as plastic, rubber as well as metals.
Also, through the injection molding process, a product is formed without the need to have it subjected to other manufacturing processes. Many of the component parts are effectively produced in this way right from tool, requiring very little further adjustments if any. This shortens production time and price, thus solidifying injection moulding like a widely used process in many industries.
Design with Confidence, and Manufacture with Ease
By partnering with Norck for injection molding design assistance, you gain:
- Faster Time to Market: Eliminate the iterative loop of prototyping, discovering flaws, and revising molds, all of which cause delays.
- Reduced Costs: Smart design at the outset prevents costly engineering changes later in the process.
- High-Quality Parts: Achieve parts that flawlessly match your functional requirements and aesthetic vision.
- Reliable Production: Mitigate risks associated with quality problems that create disruptions, returns, or even harm your brand’s reputation.
Applications of Injection Molding
Injection molding is used frequently in industries; in automobile manufactures, in medical instruments, aerospace and electronics besides the few examples stated above. For instance in the automotive industry injection molding is used to manufacture car interior such as dashboard, car bumpers and other important body parts. In the medical industry where injections molding is used most often than in any other industries is crucial due to products such as precision instruments, medical equipment and the likes.
Conclusion
Summing up, injection molding might be deemed as one of the most efficient types of the manufacturing that plays a significant role in diversified industries. One thing with injection molding is that it delivers a very high level of accuracy, consistency and can easily be scaled up for production of larger quantities of parts. Consequently, as the complexities of the parts to be manufactured by industries increases due to advancing technology and other factors, injection molding will remain essential in modern manufacturing.