Comprehensive Guide to Ball Valve Manufacturers and Valve Types
This post explores the role of ball valve manufacturers and provides insights into different valve types, highlighting their functionalities and applications across industries.
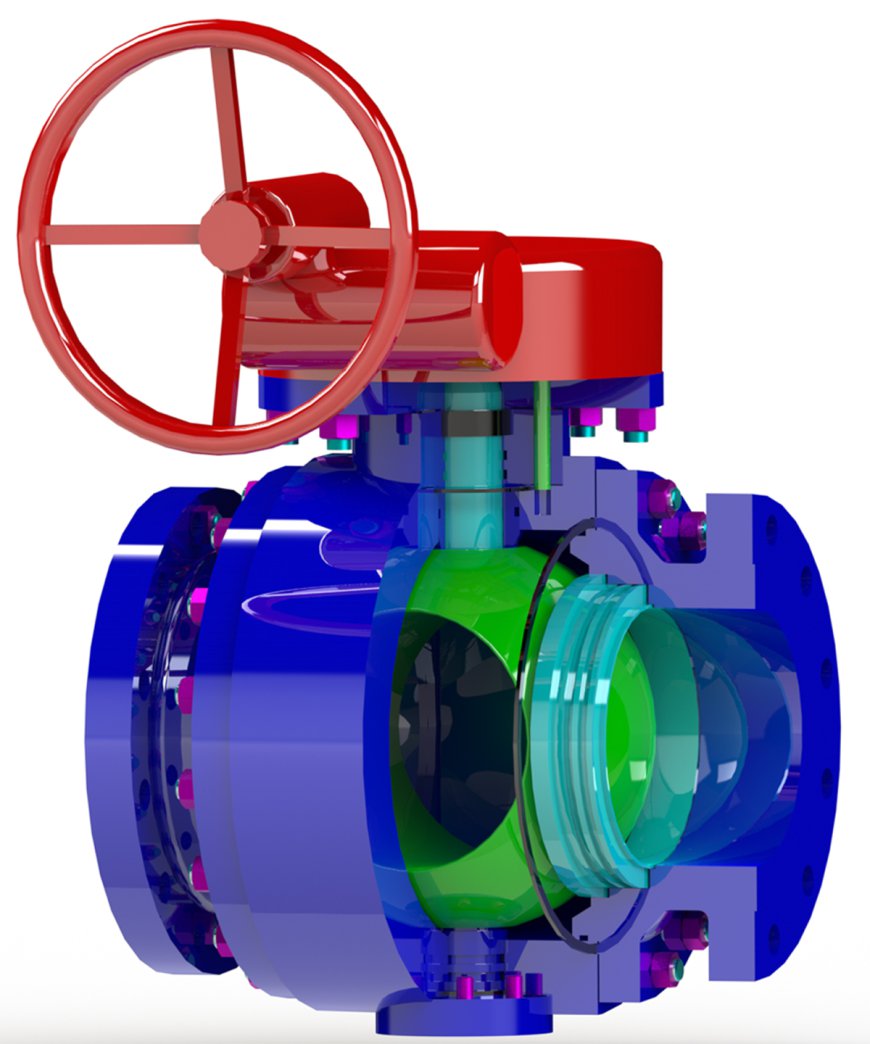
Ball valves are crucial, highly reliable, and versatile in fluid control and management in many industries. They operate effectively and are built to withstand pressure, making them suitable for everyday use in homes and industries.
Understanding Ball Valves
Balancing valves work through a sphere known as the ball, which turns on a central bore. Valve and flow path: as the figure indicates, when the hole is parallel to the flow path, fluid can flow through the hole; however, when the hole is perpendicular to the flow path of the valve, flow is inhibited. The operational mechanism is consequently rather primary, allowing immediate ball rotation and valve closing; therefore, ball valves are most suitable for applications that demand low pressure and minimal leakage.
Components of a Ball Valve
Body: Metals such as stainless steel, brass, and PVC with an integrated ball are common materials used in the manufacture of the body, which forms the foundation of the valve's structure.
Ball: A sphere within a valve or the control element that governs flow. It is usually enameled or made of a material capable of standing, withstanding rigorous corrosion, or wearing.
Seats: Seating is where the balls come into contact, providing a leak-proof hole when the valve is shut.
Stem: This coupler couples the actuator, a handle, or a gearbox to the ball and transfers the rotational motion to regulate the flow.
Actuator: How the valve is controlled, whether by hand using a lever, motorized, air pressure, or hydraulic pressure devices such as actuators.
Types of Ball Valves
Ball valves are categorized based on design and functionality, each suited for different applications where precise control over fluid flow is essential. The main types include:
Floating Ball Valves:
Design: In this type, the stem is not fixed, and there is only slight oscillation with the sealing surface of the valve seats.
Applications: Applicable in industries where pressure variety is weak or unimportant, such as home water supply and the average industrial processes.
Trunnion Ball Valves:
Design: Other globe valves have mechanical balls atop and below seats to decrease operating turning force and attain seat sealing under high pressure.
Applications: This material is highly suited for demanding high-pressure and large-diameter pressurized products such as oil and gas piping systems, refining, and petrochemicals.
Three-way Ball Valves:
Design: These valves have an L-shape or T-shape haptic ball or manifold ports that can be directed or combined through one or more inlet and outlet ports.
Applications: Applied where it is possible to control the flow direction where the flow of fluids has to be reversed or when using a mixing chamber is desirable, as in chemical processing and pharmaceutical industries.
Cavity Filled Ball Valves:
Design: Intended for applications where some fluids must be kept under low pressure inside a cavity to avoid injury or destruction of the valve.
Applications: Typically employed in services where the transported fluids have high viscosity and contain solid particles or thick slurries.
V-Port Ball Valves:
Design: It has a V-port, which offers greater control than full-port or reduced-port ball valves due to the differentiation in flow.
Applications: It is ideal for any process that demands remarkably accurate flow regulation, such as the chemical industry, water production, food preparation, and production.
Understanding Ball Valve Manufacturers
Ball Valve Manufacturer are essential in developing and providing valves to organizations and institutions with such needs across the globe. These manufacturers focus on manufacturing ball valves with an overall focus on the discipline needed to ensure the valves fit special operational conditions within various industries. The manufacturing process involves several key stages:
Design and Engineering: Manufacturing involves thorough design and engineering at the production line as its initial step. This phase involves imagining valve structures and component types and using variables such as pressure, temperature, and flow rate.
Material Selection: A valve's material selection depends on its application and the conditions required in the valve area. Stainless steel is the most frequently used material, followed by brass, bronze, and other alloys capable of withstanding corrosion and useful for long-lasting applications.
Production Techniques: Automobile technology also includes highly accurate and precise manufacturing technology. Valve parts formed through CNC machining, casting, forging, and molding have close tolerances to provide enhanced and uniform quality.
Quality Control: At every step of the process, specific measures are taken to ensure the best product quality that goes to market and meets market standards. This involves checking various aspects such as leakage, pressure, and circuit functioning.
Customization: It is also important to note that manufacturers usually create package deals that may incorporate special features to suit certain customer needs. These can comprise differences in the valve dimensions, protection coating to improve valve longevity, or overhaul changes appropriate for particular operational conditions.
Choosing the Right Ball Valve Manufacturer
Choosing the appropriate ball valve manufacturer effectively caters to the requisite characteristics, durability, and long service cycle of systems that handle fluids. Consider the following factors when choosing a manufacturer:
Experience and Reputation: You should choose a manufacturer with several recommendations and an outstanding reputation in the marketplace.
Quality and Standards: The manufacturer should implement these guidelines using API, ANSI, ISO, and ISO 9001 certifications where possible.
Customization and Support: Evaluate the manufacturer's potential to develop valves tailored to the end user's requirements and observe the company's technical assistance.
Price and Delivery: Assess the product's price sensitivity and the manufacturer's ability to deliver within the stipulated delivery period without compromising the product's quality.
Final Words
Many ball valve manufacturers are vital suppliers of these components and play a significant part in supporting the working of various fluid control industries. Each ball valve mentioned above is thus best suited for specific operations and applications to select the correct valve. Therefore, A business can work with well-established manufacturers and emphasize some of the most important and thoughtful selection parameters to increase performance, reliability, and safety in handling fluids.
By understanding the Valve Types, functionalities, and leading manufacturers of ball valves, stakeholders can make informed decisions, enhancing operational efficiency and reliability in fluid management systems.