Fixing Common Issues with Cumprasir Motor Winding: Troubleshooting and Solutions
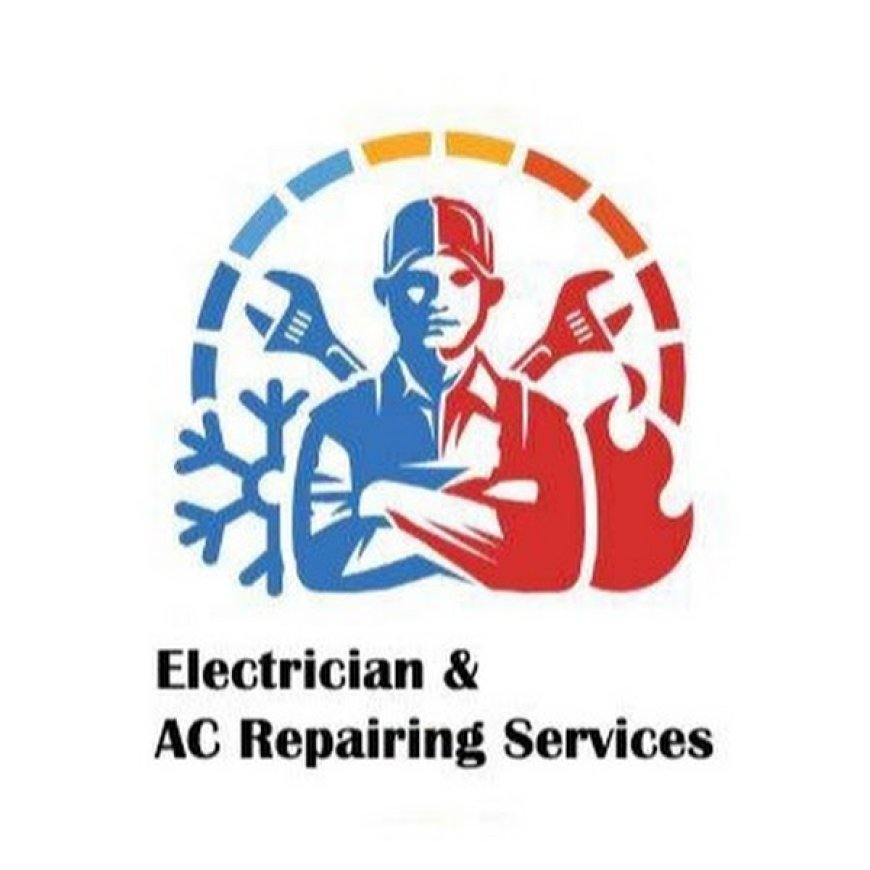
Introduction
Motor winding is a delicate and technical process that requires attention to detail, precision, and a solid understanding of electrical principles. Fix Common Issues with Cumprasir Motor Winding known for its expert services in motor rewinding, adheres to high standards of quality and performance. However, even with the best equipment and materials, issues can occasionally arise during the motor winding process. These issues can impact the motor’s efficiency, cause operational failures, or reduce its overall lifespan.
This article explores some of the most common issues faced during Cumprasir motor winding and offers practical solutions to fix them. Whether you're working on rewinding industrial motors, commercial equipment, or smaller electric motors, understanding how to troubleshoot and fix these issues will ensure the motor operates smoothly after repair.
1. Uneven or Improper Winding
Problem: One of the most common issues with motor winding is uneven winding. This happens when the coils are not wound uniformly, either in terms of spacing, tension, or coil turns. Uneven winding can lead to imbalanced motors, higher power consumption, overheating, or even failure to start.
Causes:
- Incorrect machine settings during the winding process.
- Human error or inexperience with winding techniques.
- Misalignment of the motor components (armature or stator) during winding.
Solution:
- Use Proper Equipment Settings: Ensure the winding machine is set up with correct parameters (tension, speed, coil size, etc.). Use machines with automatic tension control to maintain uniformity.
- Ensure Proper Alignment: Before starting the winding process, make sure that the armature or stator is aligned correctly within the machine.
- Monitor the Process: Pay attention throughout the winding process. Use a gauge or tool to check the uniformity of the coils regularly.
- Use Consistent Technique: If manually winding, use consistent hand pressure and speed to maintain equal tension on the wire as you wind each coil.
2. Insufficient Insulation or Poor Insulation Resistance
Problem: Insufficient insulation is a serious issue that can lead to short circuits or motor failure. The windings are coated with insulation to prevent electrical contact between the coils and the motor's core. If the insulation is poorly applied or the material is of low quality, it can result in electrical leaks, overheating, or total motor failure.
Causes:
- Poor quality or improper insulation materials.
- Incomplete varnishing or lack of proper drying time for insulation.
- Physical damage to the insulation during the winding process (e.g., wire rubbing against sharp edges or rough handling).
Solution:
- Check Insulation Material: Use high-quality insulation materials, such as durable varnishes, resin, or insulation paper. Ensure they meet the motor’s voltage and operational requirements.
- Apply Insulation Properly: After winding, make sure to apply insulation properly to all layers of the winding. Use proper tools and techniques for coating the wire with varnish or resin, ensuring that all surfaces are covered.
- Allow Drying Time: After varnishing, allow sufficient drying and curing time before reassembling the motor. Insufficient curing time can lead to incomplete insulation.
- Inspect for Physical Damage: Inspect the windings carefully for physical damage that may have occurred during handling or winding. This can include nicks or cuts in the insulation that might expose the wire to the core or other windings.
3. Incorrect Coil Count or Turns per Coil
Problem: Incorrect coil count or turns per coil can significantly affect the motor's performance. Each motor has a specific winding configuration that includes the number of turns per coil, the type of winding pattern (lap or wave), and the voltage rating. If these parameters are not correctly replicated during rewinding, the motor may operate inefficiently or fail to operate altogether.
Causes:
- Inaccurate measurements during the winding process.
- Failure to match the original winding configuration.
- Not referencing the motor's datasheet or specifications.
Solution:
- Consult Manufacturer Specifications: Always refer to the original motor specifications (found in the motor’s datasheet or repair manual). These details will include the exact number of turns per coil, the wire gauge, and the winding pattern.
- Accurate Measurement Tools: Use measuring tools to count the number of wire turns accurately. Some winding machines have built-in counters to ensure precision.
- Verify Coil Turns: After completing each coil, verify the number of turns before moving on. Mistakes can be easily missed if not checked regularly.
4. Motor Overheating After Rewinding
Problem: Overheating is a major issue that can damage both the winding and the motor’s core. When a motor runs too hot, it can burn out the insulation, degrade the copper windings, and even cause permanent damage to the bearings and other internal components.
Causes:
- Excessive Load: If the motor is operating under a load greater than its rated capacity, it will generate excess heat.
- Improper Winding or Insulation: Poor winding techniques or inadequate insulation can increase the motor's resistance, which can also result in overheating.
- Poor Ventilation: Lack of proper cooling or ventilation for the motor can cause heat buildup.
Solution:
- Ensure Proper Load Handling: Make sure the motor is not underloaded or overburdened. If the motor is operating under high stress, consider upgrading to a larger unit or balancing the load.
- Verify Coil Resistance: Check the coil resistance after rewinding. If the motor’s resistance is too high, it may indicate a problem with the winding (such as poor insulation or too many turns).
- Improve Ventilation: Ensure that the motor has adequate ventilation for cooling. Use fans or cooling systems if needed, especially for large industrial motors.
- Test Under Load: After rewinding, perform tests to ensure that the motor operates within its specified parameters. This can help identify issues related to overheating before they become more serious.
5. Motor Not Starting or Low Torque
Problem: A motor that doesn’t start properly or has low torque after rewinding may be caused by electrical issues in the windings, poor connections, or mechanical faults.
Causes:
- Electrical Short Circuits: Incorrect winding, poor insulation, or a broken connection can cause a short circuit, preventing the motor from starting.
- Open Windings: If a winding is improperly connected or a coil is open, the motor may not run or may run with reduced torque.
- Incorrect Commutator or Rotor Alignment: For motors with a commutator (like DC motors), improper alignment or worn-out brushes may prevent proper motor operation.
Solution:
- Check Continuity: Use a multimeter to check for continuity in the windings. Ensure that all coils are connected and free from open circuits.
- Inspect Commutator and Brushes: In motors with a commutator, check for wear on the commutator and brushes. If they are worn out, replace them.
- Check Motor Connections: Ensure that all connections are secure and that there are no loose wires or terminals that could cause starting issues.
- Verify Rotor Alignment: Ensure that the rotor is correctly aligned within the motor. A misaligned rotor can create friction and prevent the motor from starting properly.
6. Motor Vibration or Noise
Problem: Excessive vibration or noise can be a sign of mechanical or winding issues. If the coils are not wound correctly, or if there is an imbalance in the motor, the motor may produce unwanted vibrations or noise during operation.
Causes:
- Imbalance in Winding: Uneven windings can cause the rotor or stator to become unbalanced, leading to vibrations.
- Loose Parts: Loose windings, damaged bearings, or an improperly fitted rotor can contribute to motor vibrations.
- Motor Misalignment: If the rotor is misaligned within the stator, it can create mechanical friction, causing vibration and noise.
Solution:
- Balance the Windings: Ensure that the windings are evenly spaced and that each coil is wound with consistent tension. This helps maintain balance in the motor.
- Check Rotor and Stator Alignment: Ensure that the rotor is aligned properly within the stator, and that all moving parts are secured and properly lubricated.
- Inspect Bearings: Check the motor bearings for wear and replace them if necessary. Worn bearings can contribute to vibration and excessive noise.
Conclusion
Master Cumprasir Motor Winding involves understanding common issues that can arise during the rewinding process and knowing how to address them effectively. By following the troubleshooting solutions outlined above, you can fix common motor winding problems, ensuring that your rewound motors perform optimally, efficiently, and reliably. Regular maintenance, careful attention to detail, and adherence to best practices in motor winding will help extend the lifespan of motors and reduce the likelihood of future problems.