How Petroleum Testing Equipment Improves Fuel Quality
Discover how petroleum testing equipment enhances fuel quality by ensuring accuracy, safety, and compliance with industry standards.
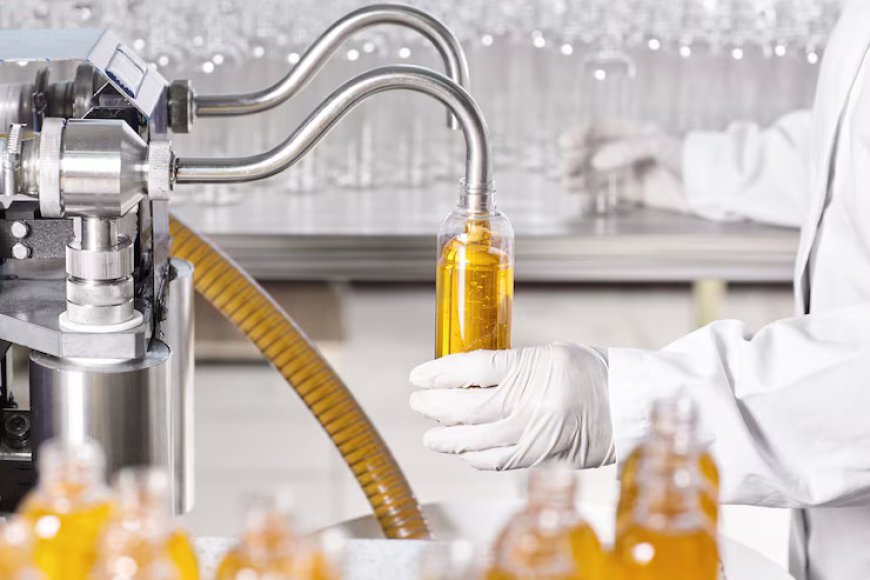
In today’s rapid world, quality matters more than quantity. The quality of fuel has an important role in the longevity and performance of the engines across industries. It has become necessary to make sure the quality of petroleum products improves as the technology develops and an ever-growing demand for cleaner increases the efficiency of the fuel. And here comes the excessive need for petroleum testing equipment. To maintain fuel standards and improve the effectiveness, safety, and environmental impact of fuels, high-quality testing equipment from reliable petroleum lab testing equipment suppliers is essential.
In this article, we'll look at how petroleum testing equipment works, how important it is in guaranteeing gasoline quality, and the various types of equipment that meet different testing criteria.
The Role of Petroleum Testing Equipment in Fuel Quality
Equipment petroleum testing is designed to analyze the physical and chemical properties of fuels and oils. Key elements, including quality control, pollutant identification, regulatory compliance, and performance optimization, are all evaluated with the use of this equipment. In order to comply with gasoline quality regulations in the automobile and aviation industries, this testing apparatus is essential.
Petroleum lab testing equipment reduces the risks associated with low gasoline quality by comparing the fuel’s quality to the required consumption criteria. The information gathered from these tests enables fuel producers, refineries, and end users to make well-informed decisions that, in the end, reduce emissions, prevent engine damage, and increase fuel efficiency.
Advantages of Petroleum Testing Equipment
Investing in petroleum testing equipment provides several benefits, especially for sectors where gasoline quality is essential. Let’s explore a few of these benefits:
1. Improved Engine Performance: Testing apparatus can identify contaminants and guarantee that fuels are refined to satisfy particular requirements, which eventually improve engine longevity and performance.
2. Safety Assurance: Hazardous circumstances like engine failures or fires might result from low-quality fuel. Testing equipment aids in ensuring fuel safety by detecting and removing hazards.
3. Environmental Protection: Emissions are influenced by fuel quality. By confirming that fuel satisfies environmental regulations, testing equipment helps prevent hazardous emissions.
4. Cost savings: By lowering the chance of damage to equipment and automobiles, routine testing prolongs engine life and lowers maintenance expenses.
5. Regulation Compliance: Strict laws governing gasoline quality, particularly in relation to emissions, are in place in many nations. By ensuring that petroleum products fulfill certain regulatory requirements, testing helps avoid penalties and legal problems.
Types of Petroleum Testing Equipment and Their Functions
Many kinds of petroleum testing equipment are available to assess components of fuel quality. Below are some of the most essential types of testing equipment:
1. Equipment for Testing Grease and Oil
Determining the amount of oil and grease present in petroleum products requires the use of oil and grease testing equipment. This apparatus determines the concentration of non-volatile, oil-based compounds in samples, which is essential for evaluating the environmental effect and product quality.
An excessive amount of oil and grease can cause engine damage, higher emissions, and poor combustion efficiency.
Frequently utilized in businesses that significantly depend on oil-lubricated machinery, environmental testing, and fuel quality monitoring.
2. Density meters
Density meters measure a fuel sample’s mass per unit volume. Fuel’s density and energy content are intimately correlated, which affects efficiency and performance.
Density measurement, which guarantees that it satisfies industrial requirements and operates effectively in a range of circumstances assesses fuel quality.
Frequently utilized in fuel testing for automobiles, ships, and airplanes.
3. Flash tester Point
Flash point testers measure the temperature at which a fuel can evaporate and turn into an ignitable mixture in air. This test is essential for identifying petroleum products’ flammability and is important for maintaining safety.
Because lower flash points increase the risk of ignite, knowing the flash point is essential for handling, storing, and transporting gasoline safely.
Frequently used for evaluating petroleum-based materials such as fuel and lubricants.
4. Measurements of Viscosity
A petroleum product’s thickness or fluidity can be measured with a viscosity meter. Viscosity influences an engine’s performance and efficiency by affecting how well fuel flows through it.
Prevents wear and tear by ensuring the fuel has the right viscosity to operate best with particular cars and machines.
Mainly utilized for evaluating industrial lubricants, automobile fuels, and aviation fuels.
5. Testers of Distillation
Distillation tests assess a fuel’s boiling range properties. This data aids in predicting the fuel performance at different temperatures.
Evaluates the stability and appropriateness of fuel for various operating circumstances and climates.
Used to test aviation fuels, diesel, and gasoline to make sure they work well in a range of temperatures.
6. Sulfur Content Analyzers
Sulfur content analyzers are designed to measure the amount of sulfur in fuels. Excess sulfur leads to harmful emissions, making it essential to maintain low sulfur levels, especially in fuels for vehicles.
Reducing sulfur content in fuels is crucial for minimizing air pollution and meeting environmental regulations.
Used in a wide range of refineries and labs focused on environmental protection.
Importance of Regular Fuel Testing in Maintaining Quality Standards
Regular fuel testing is essential to maintaining high-quality standards. The following are some reasons why consistent testing is crucial:
1. Detecting Contaminants Early: Regular testing helps in the early detection of impurities or unwanted substances in fuel, preventing issues before they arise.
2. Ensuring Product Consistency: Consistent testing ensures that each batch of fuel meets the same high standards, leading to reliable product performance.
3. Improving Operational Efficiency: Better fuel results in more effective operation, which lowers engine wear and tear and lowers maintenance expenses.
4. Protecting Brand Reputation: Suppliers can enhance their brand’s reputation and foster trust by continuously producing high-quality goods.
Regular fuel testing also demonstrates a commitment to safety and environmental responsibility, as it ensures that products align with industry standards and regulations.
Conclusion:
Petroleum testing equipment is essential for guaranteeing gasoline purity, improving engine efficiency, maintaining safety, and lessening the impact on the environment. Equipment like viscosity meters, flash point testers, and oil and grease testing equipment provides a thorough approach to fuel analysis, assisting businesses in meeting performance and regulatory requirements. When sourcing such tools, it's crucial to work with a reliable petroleum lab testing equipment supplier to ensure high-quality and accurate results, vital for both operational success and compliance with industry standards.
The road to improved fuel quality is obvious if you have the proper petroleum testing apparatus. Companies may positively affect industry standards and environmental goals by prioritizing quality testing, demonstrating that high-quality gasoline is about more than just performance—it’s about responsibility.