How to Choose the Right Anilox Coating Attachment for Your Printing Process?
An anilox roller, which transfers the coating substance, and a metering blade, which guarantees the proper quantity of coating is applied, are the common components of the coating attachment. The arrangement of these parts can change based on the particular printing press and use.
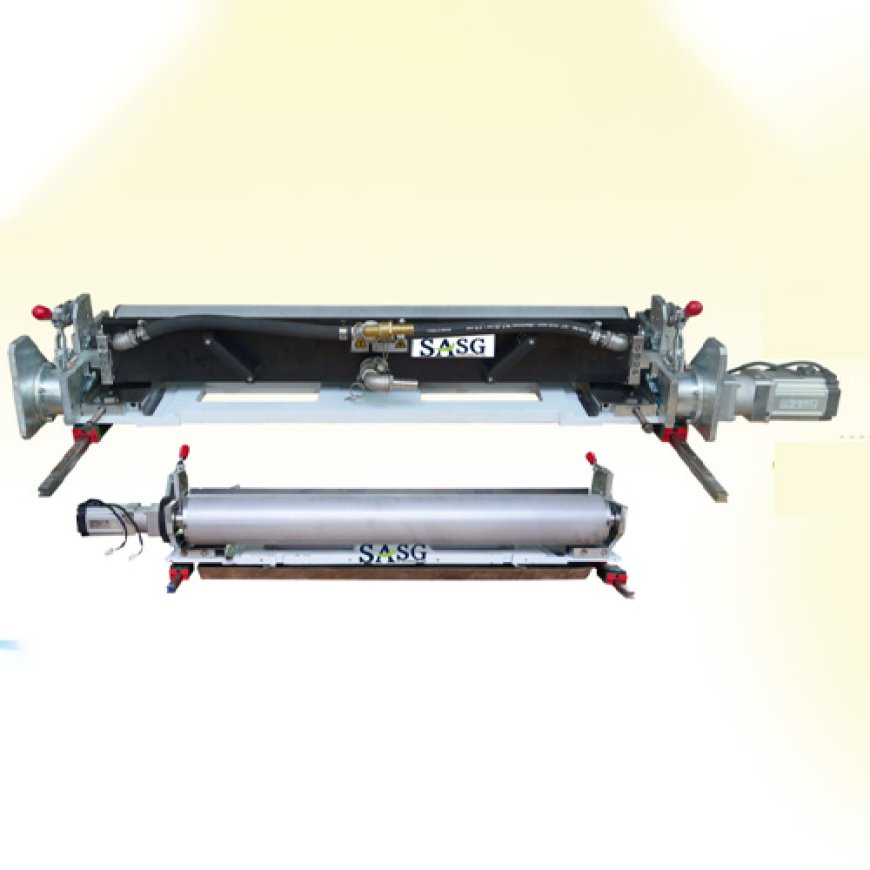
An anilox roller is crucial to the print quality in the flexographic printing industry. In order to guarantee that the print has the appropriate color, texture, and sharpness, it is the part that regulates the supply of ink and coating to the substrate. While choosing the right anilox roller for ink application receives a lot of attention, the Anilox Coating Attachment is a crucial but frequently disregarded step in the procedure.
When working with coatings, varnishes, and other finishing applications, selecting the appropriate Anilox Coating Attachment is important for producing prints of consistently high quality. The correct coating attachment guarantees that your output is perfect and satisfies both functional and aesthetic criteria, whether you're printing on labels, packaging, or other materials. The process of choosing the best anilox coating attachment for your printing requirements will be explained in this blog.
What Is an Anilox Coating Attachment?
It's important to understand the definition of an Anilox Coating Attachment and its function in printing before beginning the selecting process. An important part of a flexographic printing press that is in charge of coating or finishing the printed substrate is the Anilox Coating Attachment. Coating attachments are made specifically for applying extra coating layers, such matte, gloss, or protective finishes, whereas conventional flexographic presses focus on applying ink.
An anilox roller, which transfers the coating substance, and a metering blade, which guarantees the proper quantity of coating is applied, are the common components of the coating attachment. The arrangement of these parts can change based on the particular printing press and use.
Depending on the coating type and the properties of the printed substrate, there are several kinds of anilox coating attachments. The final look and functionality of the print can be greatly influenced by the choice of coating attachment, which guarantees consistency, precision, and quality in each application.
Factors to Consider When Choosing an Anilox Coating Attachment
There is no one-size-fits-all solution when it comes to selecting the ideal anilox coating attachment for your printing requirements. Depending on the particular kind of coating, substrate, and printing press you are employing, a number of parameters need to be taken into account. These elements consist of:
1. Type of Coating or Varnish
Choosing the type of coating or varnish you'll be using is the first step in choosing the best anilox coating attachment. Specialized anilox rollers and attachments are needed for various coating types, including solvent-, water-, and UV-based coatings, because they have varying viscosities, curing processes, and performance characteristics.
Water-based coatings: Label printing and packaging both frequently use these coatings. They usually have a higher viscosity and are less harmful to the environment than solvent-based coatings. An anilox roller with the right cell count and volume is necessary for water-based coatings in order to guarantee that the right amount of coating is applied.
UV coatings: UV coatings provide the substrate's surface a firm finish by curing under ultraviolet light. An anilox roller with a particular cell geometry is frequently needed for these coatings in order to guarantee accurate application and rapid drying under UV light. Generally, coating attachments for UV processes must be able to handle the high-speed production processes typical of UV printing and work with formulations that dry quickly.
Solvent-based coatings: Because of environmental concerns, solvent coatings are less widespread, however they are still utilized in some applications. These coatings need an anilox roller that can provide precise control over coating application because they frequently have a lower viscosity than water-based coatings.
2. Viscosity of the Coating
Another important consideration for selecting the appropriate anilox coating attachment is the coating's or varnish's viscosity. The choice of the anilox roller's cell count and volume is directly influenced by the coating material's viscosity, which is defined as its thickness or flow properties.
- An anilox roller with deeper cells is necessary for high-viscosity coatings (such UV coatings) in order to handle the thicker substance. A larger coating volume can be applied to deeper cells, guaranteeing even coverage with less waste.
- An anilox roller with smaller cells is necessary for low-viscosity coatings (such water-based coatings) in order to avoid overapplication and guarantee accurate control. Because these coatings are more fluid, they work better on smaller cells, guaranteeing that the proper amount of material is coated.
Issues like uneven coating application, coating streaks, or excessive waste might arise from selecting the incorrect roller for a particular viscosity, which can impair print quality and production efficiency.
3. Cell Geometry
The geometry of the anilox roller’s cells is another important consideration. The type of coating you're using can influence the type of cell geometry required for optimal application. Some common cell geometries include:
- Hexagonal cells: These are the most commonly used cell geometries. They offer uniform cell distribution and are suitable for a wide variety of applications. For most coatings, hexagonal cells are a safe choice, ensuring even application and reducing the risk of visible defects.
- Diamond-shaped cells: These cells are ideal for high-viscosity coatings, such as UV inks and varnishes. They are designed to deliver precise amounts of material with minimal wastage, making them perfect for applications where high control over the coating thickness is essential.
- Round cells: Round cells are often used for special applications that require more volume to be applied. They are suitable for applications where a heavier coat is necessary but can also result in higher waste and less precision in coating thickness.
The choice of cell geometry will depend on the type of coating, substrate, and desired finish. The right geometry ensures optimal performance and prevents potential coating defects, such as streaking, inconsistent coverage, or excessive buildup.
4. Coating Volume and Transfer Efficiency
- Anilox rollers vary in their ability to transfer coating material to the substrate, and this ability is typically measured in terms of volume. The volume is determined by the number of cells per inch (cpi) and the depth of the cells.
- Higher volume rollers are typically required for applications where a thicker or more generous layer of coating is needed, such as with glossy finishes or high-opacity coatings. These rollers have larger, deeper cells that hold more coating material and ensure an even transfer.
- Lower volume rollers are better suited for applications where a thinner, more controlled layer of coating is needed. For example, delicate finishes or when applying coatings to sensitive substrates may require a roller with lower volume, which results in thinner, more even coverage.
It’s important to balance volume with transfer efficiency. A higher volume roller with poor transfer efficiency can lead to overspray or waste, while a lower volume roller may not apply enough coating to achieve the desired finish.
5. Substrate Type
Different substrates (paper, film, foil, etc.) require different approaches when it comes to coating application. The nature of the substrate, such as its absorbency, texture, and flexibility, will influence the choice of anilox coating attachment.
- Porous substrates (such as paper) tend to absorb coatings more easily, so a roller with higher cell volume and deeper cells may be needed to compensate for absorption.
- Non-porous substrates (such as films or foils) tend to resist absorption, meaning that less coating material may be required, making a roller with a finer cell structure more appropriate.
Choosing the right anilox coating attachment for the substrate helps ensure that the correct amount of coating is applied without waste or oversaturation.
6. Speed and Production Volume
The printing speed and production volume of your press are additional factors to consider. Anilox coating attachments are designed to work at specific speeds, and their performance can be affected by high-speed operation.
If your printing process involves high-speed production, you’ll need an anilox coating attachment that can consistently deliver accurate coating application at those speeds without compromising quality. A press that operates at higher speeds may require an attachment with specialized coatings or rollers that are designed to maintain accuracy at those speeds.
7. Press Configuration and Compatibility
Lastly, the compatibility of the anilox coating attachment with your press configuration is a critical factor. Not all coating attachments are designed to work with all types of flexographic presses. It's important to verify that the attachment you choose will integrate seamlessly with your press, considering factors like:
- The size and design of the roller and blade assembly
- The speed capabilities of the press
- The automation features available on the press
- Many modern flexographic presses come with adjustable anilox coating attachments that can be fine-tuned to accommodate various types of coatings and substrates. These customizable options allow you to adapt to a wider range of applications and reduce downtime caused by manual adjustments.
Conclusion
Choosing the right anilox coating attachment for your printing process is important for guaranteeing reliable, high-quality output. The right connection maximizes efficiency and production speed while providing ideal coating application and avoiding problems like overspray, waste, and flaws.
You can choose an anilox coating attachment that will improve print quality and reduce operational problems by carefully weighing variables including coating type, viscosity, cell geometry, substrate type, and production volume. Keep in mind that choosing the appropriate attachment for your printing process improves the overall look and usability of your printed goods in addition to saving time and money.