How to Ensure Quality and Performance with Flowable Fill Concrete?
Discover how to ensure quality and performance with flowable fill concrete through effective mixing, placement, and curing techniques for optimal results.
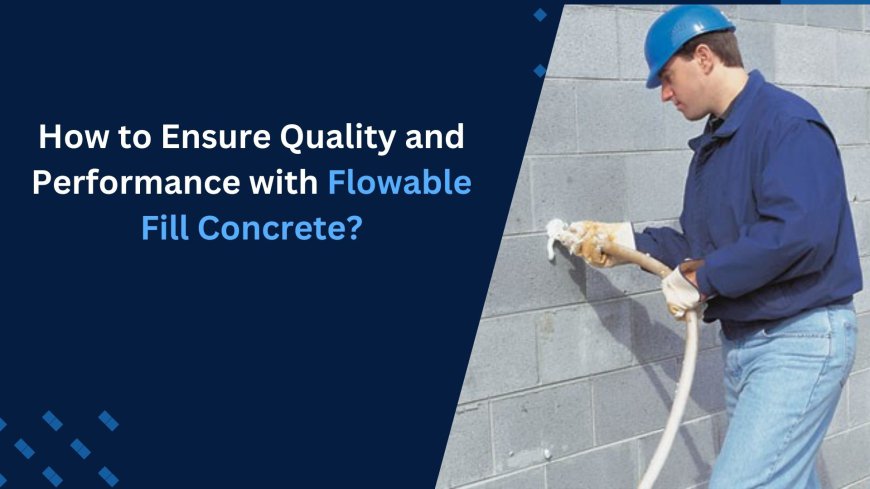
The CLSM concrete, called Flowable fill concrete, is a product that is very vital as a backfilling product as well as filling voids and as a subbase. It offers some advantages over standard compacted fill materials such as ease of installation, shorter installation time, and hence less cost incurred in the hiring of installation workers. Nevertheless, to realize these benefits and achieve quality and performance, several factors have to be taken into account. In this article, an effort will be made to identify and discuss the guidelines of quality and performance that may be used when handling flowable fill concrete.
What Is Flowable Fill Concrete?
Flowable fill concrete is a poured self compacting concrete that can be applied as a fine aggregate, water, cement, and in some instances, fly ash or other materials as well. It is often used as an alternative to compacted soil or granular backfill if compaction of fill material is either difficult or requires considerable time. Due to this flexibility, it does not need to be vibration and tamped to achieve compaction, thus can be used for utility trenches backfill, pipe bedding, and foundation support.
Benefits of Flowable Fill Concrete
Before discussing how to ensure quality and performance, it's important to grasp the primary advantages of flowable fill concrete:
Ease of Use
Flowable fill is extremely easy to work with and does not need to be compacted by hand.
Reduced Labor Costs
The fact that it is a self-compacting material means fewer people are necessary as well as less time.
Faster Installation
It means that it facilitates speedy placement thus implying that its projects shall be accomplished within the shortest time possible.
Low Permeability
It lessens the probability of allowing water leakage making it a great material to use where there is concern of water contact.
Environmentally Friendly
Such wastes have proved useful in construction activities and provide support to sustainability goals.
Factors Affecting Quality and Performance
Flowable fill concrete is characterized by high workability and low strength, and its quality and performance crucially depend on several factors. Here's what you should concentrate on throughout the manufacture, installation, and curing stages:
1) Proper Mix Design
It required a well-balanced mix design to obtain the desirable results. It is also important to mention that flowable fill usually contains a lower strength than conventional concrete; it is used for applications where an area may need to be excavated in the future. Here are some strategies to ensure the correct balance:
Use Quality Materials
As for aggregates, materials should be clean fine ones, while cement together with fly ash, if used, should also meet the requirements.
Control Water Content
Too much water can cause the substance to be less strong also little water can make the compound to be less smooth.
Additives
It emerges that workability can also be enhanced by using additives such as water reducers and plasticizers without necessarily having to introduce more water into the mix.
2) Testing Before Placement:
To ensure that the flowable fill mixture gives the required performance it has to be tried before use on a large scale. This involves
Slump Flow Test
This test ensures the preservation of the substance of the show and rapid switching between the two programs. It should be a thin consistency, not leaky where some portions will drip out leaving the other components.
Compressive Strength Testing
Perform density and compressive strength tests to verify that the material has adequate strength as regards its application. Flowable fill normally has an average compressive strength of between 50 and 150 pounds per square inch.
3. Proper Placement Techniques
Once the mix design has been decided, how you position the flowable fill is also important for ensuring performance:
Avoid Overwatering
The above conditions might give rise to segregation and low strength in the composite if overwatered. Make sure of water content before putting.
Uniform Placement
The material to be packed should be placed consistently and uniformly because the presence of air pockets or other discrepancies within the fill material is not allowed.
No Manual Compaction
Flowable fill should not be mechanically compacted because they have this peculiar characteristic of self-leveling, this will eliminate any voids that may have been made.
Common Issues and Solutions
Although flowable fill concrete is relatively simple to use, several problems may arise. Understanding these challenges and how to address them will result in a higher-quality output:
1) Segregation:
Issue:
Sometimes water content is too high or used inappropriately, the accumulations lose their bond and can no longer be bonded to the mix.
Solution:
Take care that the samples consist of sufficient water for analysis and refrain from drip positioning from a considerable distance during the place.
2) Delayed Set Time
Issue:
This can render the project time-consuming and could be occasioned by low temperatures or the use of aggressive retarding admixtures.
Solution:
During very cold climatic conditions, either change the mix design or use accelerating admixtures to enable the process to set.
3) Strength Too High
Issue:
Original flowable fill that develops strength may become very challenging to remove in the future.
Solution:
Reduce cement content and do not use some elements that can have high strength, for example, silica fume.
4) Cracking
Issue:
This is sometimes brought about by inadequate curing or by exposure to harsh conditions.
Solution:
They require that the surface should not dry quickly and that curing processes should be appropriately used on the surface.
Best Practices for Long-Term Durability
To ensure that your flowable fill lasts for years, it's important to follow these best practices:
Monitor Environmental Conditions:
When placing and curing it should be considered in terms of conditions of temperature humidity and wind.
Use Reputable Suppliers:
Mix design is made consistent and problems are avoided when quality raw materials from reliable manufacturers are employed.
Collaborate with Experts:
Professional advice from a civil engineer, concrete contractor, or a specialized testing agency may be of great help in ascertaining that the material fully meets project requirements.
Conclusion:
Coarse fill concrete is ideal for backfilling and void filling because of its ease of placing, its ability to consolidate itself and it is environment friendly. However, in order to maintain this quality as well as the defined efficiency, proper mix design, proper placement of the concrete, and sufficiently proper curing are required. It is, therefore, advised to adhere to the best practices highlighted in this article by practitioners in the building construction industry to realize much more consistent and long-term performance of the flowable fill on structural plans.
Regardless of whether you have a small utility trench itself or a massive infrastructure undertaking, knowing the proper method to use with flowable fill concrete will pay handsome dividends in terms of efficiëncy and expense control while supplying the life-cycle durability your project requires.