How to Fix Hydraulic System Failures in Heavy Equipment
Learn how to troubleshoot and fix hydraulic system failures in heavy equipment. Visit pdfmanualsshop.com for detailed repair manuals and maintenance tips.
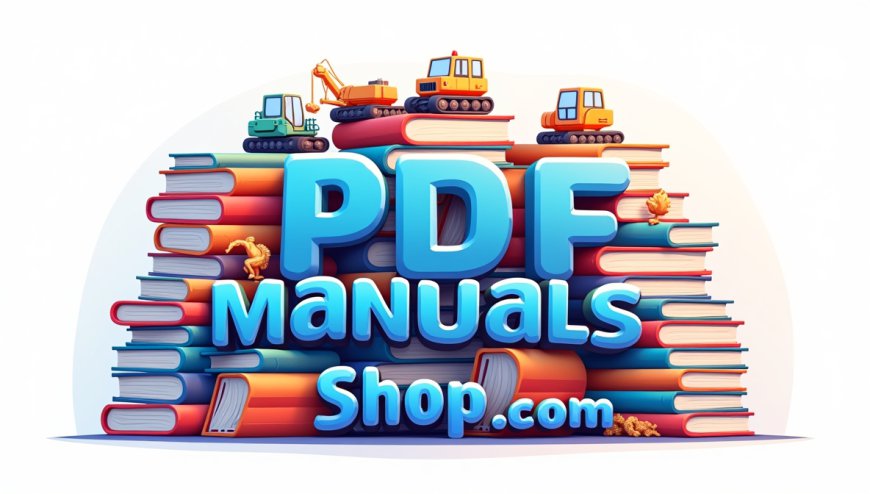
Hydraulic systems are crucial for the operation of heavy equipment, as they power various components such as the boom, blade, and other attachments. However, hydraulic system failures can lead to significant downtime and costly repairs. Understanding the common causes and knowing how to troubleshoot and repair these issues can help keep your equipment running efficiently. Let’s explore some typical hydraulic system problems and solutions.
1. Low Hydraulic Fluid Levels
Low hydraulic fluid levels can cause the system to lose pressure, resulting in sluggish or unresponsive equipment.
How to Fix It:
Check the hydraulic fluid level using the dipstick or sight gauge on the reservoir. If the fluid level is low, refill it with the manufacturer-recommended hydraulic fluid. Be sure to check for leaks in hoses, fittings, and seals, as these can cause fluid loss. Repair or replace any damaged components to prevent further leakage.
Pro Tip: Regularly inspect and maintain fluid levels to ensure optimal system performance.
2. Contaminated Hydraulic Fluid
Contaminated hydraulic fluid, caused by dirt, debris, or water, can lead to component wear and system failure.
How to Fix It:
Drain and replace the contaminated hydraulic fluid with clean fluid. Replace the hydraulic filters and inspect the system for sources of contamination, such as damaged seals or cracked hoses. Regularly schedule fluid and filter changes to maintain a clean hydraulic system.
Pro Tip: Use high-quality hydraulic fluid and filters to prevent contamination and extend system life.
3. Air in the Hydraulic System
Air trapped in the hydraulic system can cause spongy or erratic operation, as well as increased wear on components.
How to Fix It:
Bleed the hydraulic system to remove any trapped air. This process involves loosening the bleed screws on the hydraulic cylinders and operating the system to push out air bubbles. Tighten the bleed screws once the fluid flows without bubbles. Ensure all connections are tight to prevent air from entering the system.
Pro Tip: Regularly check for and remove air from the hydraulic system to maintain smooth operation.
4. Worn or Damaged Hydraulic Pump
The hydraulic pump is the heart of the system, generating the pressure needed to power the equipment. A worn or damaged pump can lead to decreased performance or complete system failure.
How to Fix It:
Listen for unusual noises from the hydraulic pump, such as whining or grinding. Check the pump’s output pressure with a pressure gauge. If the pressure is below the manufacturer’s specifications, the pump may be worn or damaged. Replace the hydraulic pump with a new or rebuilt unit that meets the manufacturer’s specifications.
Pro Tip: Regularly inspect and maintain the hydraulic pump to ensure consistent system performance.
5. Leaking Hydraulic Hoses or Fittings
Leaks in hydraulic hoses or fittings can cause a loss of pressure and fluid, leading to poor system performance.
How to Fix It:
Inspect all hydraulic hoses and fittings for signs of wear, cracks, or leaks. Replace any damaged hoses or fittings with new ones that match the system’s specifications. Tighten loose fittings and use thread sealant where necessary to prevent future leaks.
Pro Tip: Regularly inspect and replace worn or damaged hoses and fittings to prevent hydraulic system failures.
6. Faulty Hydraulic Cylinders
Hydraulic cylinders convert fluid pressure into linear motion. Faulty cylinders can result in slow or uneven movement of equipment components.
How to Fix It:
Check the hydraulic cylinders for signs of leaks, such as fluid seeping around the cylinder seals. Inspect the cylinder rods for bends, cracks, or corrosion. Replace the seals or the entire cylinder if necessary. Ensure the cylinders are properly aligned and mounted.
Pro Tip: Regular maintenance and timely replacement of cylinder seals can prevent costly repairs and downtime.
7. Overheated Hydraulic System
Overheating can cause hydraulic fluid to degrade, leading to reduced efficiency and potential system damage.
How to Fix It:
Check the hydraulic fluid temperature with a thermometer or by monitoring the system’s temperature gauge. Ensure the cooling system, such as the hydraulic oil cooler, is clean and functioning properly. Clean any debris from the cooler fins and check for blockages in the coolant lines. Replace the hydraulic fluid with one that has a higher viscosity rating if overheating persists.
Pro Tip: Keep the hydraulic system clean and free from debris to prevent overheating and maintain efficient operation.
8. Incorrect System Pressure
Incorrect system pressure can cause hydraulic components to operate inefficiently or fail prematurely.
How to Fix It:
Use a pressure gauge to check the system’s operating pressure. Adjust the pressure relief valve according to the manufacturer’s specifications. If the pressure cannot be adjusted to the correct level, inspect the relief valve for wear or damage and replace it if necessary.
Pro Tip: Regularly check and adjust the system pressure to ensure it operates within the recommended range.
Conclusion:
Hydraulic system failures in heavy equipment can be costly and time-consuming, but they are often preventable with regular maintenance and timely repairs. By addressing issues such as low fluid levels, contamination, air in the system, and worn components, you can keep your hydraulic system running smoothly. For detailed troubleshooting guides and repair manuals, visit pdfmanualsshop.com, where you can find comprehensive resources to help maintain and repair your heavy equipment.