Improving Production Outcomes with Specialized Manufacturing Software
Learn how specialized manufacturing software improves production outcomes by increasing efficiency, reducing costs, and optimizing processes.
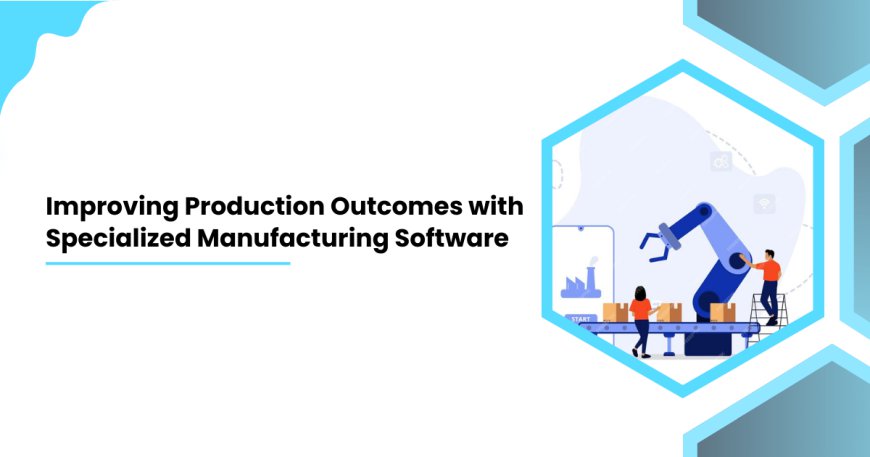
According to recent studies, manufacturers using specialized software solutions report a 20-30% increase in operational efficiency and up to a 15% reduction in production costs. In today’s competitive manufacturing landscape, leveraging such software can significantly enhance production outcomes. Manufacturing Software Development Companies are playing a crucial role in this transformation, offering tools that streamline processes, boost efficiency, and drive growth. This article explores the importance of using specialized manufacturing software, its key features, and the tangible benefits it provides to businesses.
Understanding the Role of Manufacturing Software Development Companies
Manufacturing Software Development Company play a crucial role in helping manufacturers optimize their operations by offering specialized software solutions. These companies understand the unique challenges faced in the manufacturing environment and create software tailored to address these specific needs. From managing inventory to optimizing production schedules, their software solutions provide manufacturers with a competitive edge.
Key Features:
1. Customizable Solutions: Tailored to Specific Industry Needs
-
Adaptability to Unique Manufacturing Requirements: One of the primary advantages of manufacturing software is its ability to be customized according to the specific needs of different industries. For example, a company in the automotive sector may have different requirements compared to a pharmaceutical manufacturer. The software can be customized to accommodate specific processes such as quality control, compliance management, and supply chain optimization. Customizability ensures that manufacturers can address their unique challenges effectively, leading to increased efficiency and reduced operational costs.
-
Scalability: As businesses grow, their needs evolve. Customizable software allows manufacturers to scale their operations without having to overhaul their systems entirely. The software can be adjusted to handle larger volumes of production, manage more complex data, and integrate new technologies as they become available. This flexibility makes it easier for manufacturers to adapt to changing market conditions and expand their operations smoothly.
2. Integration Capabilities: Seamlessly Connecting with Existing Systems for Better Data Flow
-
Seamless Integration with Legacy Systems: Manufacturing companies often have existing systems in place, such as Enterprise Resource Planning (ERP) systems, Customer Relationship Management (CRM) software, or legacy Manufacturing Execution Systems (MES). The right manufacturing software can integrate smoothly with these systems, ensuring a seamless flow of data across all platforms. This integration reduces the need for manual data entry and minimizes errors that can arise from disconnected systems.
-
Real-Time Data Sharing: Integration capabilities allow real-time data sharing across different departments within a manufacturing facility. For instance, the software can link production data with inventory management systems, providing a holistic view of operations. This integration helps in making timely decisions about resource allocation, reducing production bottlenecks, and optimizing inventory levels.
3. Scalability: Grows with the Business to Accommodate Future Needs
-
Future-Proofing: One of the critical features of specialized manufacturing software is its scalability. As manufacturers grow, their software needs to grow with them. Scalable solutions ensure that the software can handle increased production volumes and more complex processes without requiring a complete system overhaul. This feature is particularly important in industries where rapid technological advancements are common.
-
Flexibility for Expansion: Scalable software allows manufacturers to easily add new features or functionalities as their operations expand. For example, integrating advanced analytics for predictive maintenance or incorporating IoT devices for smart manufacturing becomes simpler with scalable software. This adaptability enables manufacturers to stay ahead of the competition and meet customer demands more effectively.
4. User-Friendly Interface: Designed to Be Intuitive, Reducing the Learning Curve for Employees
-
Ease of Use: A user-friendly interface is crucial for the successful adoption of manufacturing software. Even the most advanced software can become a barrier if it’s not easy to use. A well-designed interface minimizes the learning curve for employees, reducing the time it takes for them to become proficient with the system.
-
Reduced Training Time: Intuitive interfaces allow employees to quickly grasp the essential functions of the software, which can lead to faster implementation and improved productivity. The software’s user-friendly nature encourages staff to engage more with the system, leading to better data input and utilization. For instance, an operator can easily track production status, manage inventory, and generate reports without extensive training.
How Specialized Manufacturing Software Enhances Production Outcomes
Specialized manufacturing software goes beyond mere automation; it transforms the way manufacturers operate. By integrating various functions into a single platform, these tools provide real-time data and insights that help in making informed decisions.
-
Enhanced Efficiency: Automation reduces manual tasks, freeing up resources for more value-adding activities.
-
Real-Time Monitoring: Track production in real-time, allowing for quick adjustments to schedules and processes.
-
Improved Accuracy: Reduce human errors in data entry and processing, ensuring high accuracy in inventory and production management.
-
Increased Flexibility: Adapt quickly to changes in market demands and production schedules.
Stat Insight: According to a report by McKinsey & Company, manufacturers using advanced digital technologies can achieve up to a 15% increase in production efficiency.
Key Benefits of Using Specialized Manufacturing Software
Streamlined Operations: Automation of routine tasks frees up human resources for more complex problem-solving and strategic roles. Cost Savings: Reduction in operational costs through minimized waste, increased efficiency, and predictive maintenance. Scalability: Software scales with business growth, allowing companies to manage larger volumes without a proportional increase in overhead costs. Data-Driven Decision Making: Advanced analytics provide actionable insights that drive better business decisions and strategic planning.
Selecting the Right Manufacturing Software
Choosing the right manufacturing software is a critical decision for manufacturers. It involves understanding your specific business needs and aligning them with the software’s capabilities to ensure maximum benefit. Here’s a closer look at the key considerations manufacturers should keep in mind during the selection process:
1. Functionality: Does the Software Cover All Your Production Needs?
-
Comprehensive Coverage: The primary consideration when choosing manufacturing software is whether it meets all your production needs. This includes managing inventory, production scheduling, quality control, and maintenance. Each of these areas is crucial to optimizing manufacturing operations, and the software should be able to handle them seamlessly. For instance, the software should provide tools for tracking raw material inventory, managing production schedules to meet deadlines, and monitoring product quality throughout the production process.
-
Integration with Production Processes: Beyond these basic functions, the software should integrate with other critical production processes, such as Supply Chain Management (SCM), Manufacturing Execution Systems (MES), and Enterprise Resource Planning (ERP). Integration ensures smooth data flow across different systems, reducing manual data entry and minimizing the risk of errors. A software solution that covers all these areas can significantly enhance operational efficiency and productivity.
2. Compatibility: Will It Integrate Seamlessly with Your Existing Systems?
-
Seamless Integration: Compatibility is a crucial factor to consider because it determines how well the new software will integrate with existing systems. Manufacturing environments often consist of a mix of different software and technologies. Therefore, it’s important that the new software can work harmoniously with these systems. For instance, if a manufacturer already uses an ERP system, the new software should be able to integrate with that system to avoid duplication of efforts and data inconsistencies.
-
Data Migration: Compatibility also involves the ability of the software to handle data migration smoothly from existing systems. The software should support seamless data import and export capabilities to avoid disruptions during the transition period. This includes the ability to transfer production data, historical records, and existing business logic into the new system without losing valuable information. Ensuring compatibility with existing IT infrastructure minimizes the risk of operational disruptions during the software implementation phase.
3. Customization: Can the Software Be Customized to Meet Unique Requirements?
-
Customizability: No two manufacturing businesses are exactly alike, and each has unique requirements. The ability to customize the software to meet specific needs is essential. Customization could mean modifying the software to fit unique manufacturing processes, integrating with specific equipment, or adapting reporting functionalities to align with business objectives. For instance, a manufacturer specializing in high-mix low-volume production might require software that supports flexible production schedules and customizable reporting tools.
-
Scalability: Along with customizability, scalability is another important aspect. The software should not only meet current requirements but also be able to grow with the business. This means that as the business expands, the software should be easily adaptable to accommodate new production lines, additional employees, or expanded product offerings without major reconfigurations. A scalable software solution allows manufacturers to add new functionalities over time without needing to replace the entire system.
4. Vendor Support: Is There Reliable Customer Support Available?
-
Responsive Support: Reliable customer support is crucial when selecting manufacturing software. The vendor should offer comprehensive support, including training, troubleshooting, and updates. The support should be accessible and responsive to ensure quick resolution of any issues that may arise during the software’s operation. Good vendor support can prevent minor issues from becoming major disruptions.
-
Ongoing Assistance: Beyond the initial setup, ongoing support is important. The vendor should provide regular updates and maintenance to ensure the software remains up-to-date with technological advancements and evolving industry standards. Additionally, the vendor should offer training resources to keep employees proficient with the software. This ongoing support ensures that the software continues to deliver value long after its initial implementation.
Also Read: IoT in Civil Engineering: How GPS Trackers Optimize Construction Equipment Management
Challenges in Implementing Manufacturing Software
While the benefits are clear, implementing manufacturing software can present challenges:
-
Resistance to Change: Employees may resist new software due to familiarity with older methods.
-
Integration Issues: Ensuring new software integrates smoothly with existing systems can be complex.
-
Data Migration: Moving existing data into the new system without loss or corruption can be a significant hurdle.
Stat Insight: A survey by Deloitte found that 31% of companies experienced challenges during software integration due to data migration issues.
How to Overcome These Challenges
Implementing new manufacturing software can come with its fair share of challenges. However, with the right strategies, manufacturers can overcome these hurdles and ensure a smooth transition to the new system. Here’s a detailed look at the steps manufacturers can take to overcome these challenges:
1. Provide Comprehensive Training
-
Educate Employees on the Benefits of the New System: One of the primary challenges during the implementation of new manufacturing software is user resistance due to fear of change or lack of understanding. To combat this, it is crucial to provide comprehensive training that educates employees on the benefits of the new system. This training should clearly communicate how the software will improve their daily tasks, enhance efficiency, and make their roles easier.
-
Role-Specific Training: Tailoring the training to specific roles within the organization ensures that employees understand the relevance and impact of the new software to their particular functions. For example, production managers might need training on scheduling optimization features, while quality control staff might require in-depth training on how the software improves compliance tracking and reporting.
-
Hands-On Learning: Hands-on training sessions are particularly effective. These sessions allow employees to interact with the software in a controlled environment, practice using its features, and get comfortable with its interface before it goes live. This approach can significantly reduce the learning curve and boost user confidence in the new system.
2. Seek Expert Help
-
Engage with Software Vendors: Engaging with the software vendor right from the beginning can provide manufacturers with the support they need throughout the integration process. Many vendors offer comprehensive support packages that include implementation services, ongoing technical support, and training resources. By working closely with the vendor, manufacturers can gain insights into best practices, potential pitfalls, and tips for maximizing the software’s benefits.
-
Integration Support: Software vendors often provide integration support services, which are invaluable during the implementation phase. These services may include data mapping, system setup, and connecting the new software to existing systems. The vendor’s expertise ensures that the software integrates smoothly without causing disruptions to existing operations. For instance, if a company is integrating new MES software with its existing ERP system, the vendor can provide guidance on how to synchronize these systems effectively.
-
Post-Implementation Support: Beyond initial setup, ongoing support from the vendor is crucial. This includes regular software updates, troubleshooting, and maintenance. Knowing that expert support is readily available can alleviate concerns about technical issues or software glitches, helping manufacturers maintain continuity in their operations.
3. Plan for Data Migration
-
Ensure a Robust Strategy for Transferring Existing Data Without Disruptions: Data migration is a critical step in implementing new manufacturing software. This process involves transferring existing data from legacy systems into the new software without data loss or disruption to ongoing operations. Manufacturers should develop a detailed data migration strategy to address potential challenges.
-
Data Mapping and Validation: The first step in planning for data migration is to map out the existing data structures and validate them against the new software’s requirements. This involves identifying data types, formats, and relationships to ensure the data is compatible with the new system. For instance, mapping existing customer order details to match the new system’s product and customer data requirements.
-
Test Data Migration: Before going live, manufacturers should conduct thorough testing of the data migration process. This means transferring a subset of the data and validating its integrity in the new software environment. By testing data migration in a controlled manner, manufacturers can identify and rectify any issues related to data loss, corruption, or compatibility issues before fully implementing the system. This proactive approach minimizes the risk of data disruption during the transition.
-
Establish a Backup Plan: Even with thorough testing, it’s wise to have a backup plan in place in case of unforeseen issues during data migration. A robust backup strategy ensures that data can be quickly restored to the original state if migration problems occur. This plan could involve regular backups of the current data, staging the data migration process, and maintaining a fallback system to switch back if problems arise.
Future Trends in Manufacturing Software Development
The landscape of manufacturing software is evolving rapidly, driven by advancements in technology and shifting industry demands. As manufacturers continue to embrace digital transformation, several key trends are shaping the future of manufacturing software. Here’s a closer look at these transformative trends:
1. Artificial Intelligence (AI): For Predictive Maintenance and Quality Control
-
Predictive Maintenance: One of the most significant advancements in manufacturing software is the integration of Artificial Intelligence (AI) for predictive maintenance. AI leverages data analytics to predict equipment failures before they occur. By analyzing data from sensors and other devices, AI algorithms can identify patterns that indicate potential issues, allowing manufacturers to perform maintenance proactively. For example, AI can monitor vibration and temperature data from machines to detect anomalies that may lead to breakdowns. This helps in reducing downtime, lowering maintenance costs, and extending the lifespan of equipment.
-
Quality Control: AI also plays a crucial role in enhancing quality control processes. Manufacturers can use AI-driven image recognition and machine learning algorithms to detect defects in real-time during the production process. This enables early detection of quality issues, leading to higher product quality and fewer rework costs. For instance, AI can be used in visual inspection systems to identify defects in products on the assembly line, improving overall product consistency and reducing waste.
2. Internet of Things (IoT): Integration of Smart Devices for Real-Time Monitoring and Management
-
Real-Time Monitoring: The integration of Internet of Things (IoT) devices is transforming manufacturing software by enabling real-time monitoring of production processes. IoT devices, such as sensors and actuators, are embedded in equipment to provide continuous data about the manufacturing environment. These devices can track variables like temperature, humidity, and machinery performance in real-time. The data collected can be used to optimize operations, reduce energy consumption, and improve overall efficiency. For example, IoT-enabled devices can automatically adjust production settings based on real-time data, minimizing waste and improving output quality.
-
Enhanced Decision Making: The IoT also facilitates enhanced decision-making capabilities. By collecting and analyzing data from multiple sources, manufacturers can gain deeper insights into their operations. This real-time data integration allows for predictive analytics, which can forecast demand, optimize inventory, and schedule maintenance more effectively. Manufacturers can also implement predictive analytics to monitor the health of equipment, preventing unexpected breakdowns and optimizing maintenance schedules.
3. Cloud Computing: Enables Manufacturers to Access Software from Anywhere, Facilitating Remote Work and Global Operations
-
Flexibility and Scalability: Cloud computing is another key trend shaping the future of manufacturing software. It enables manufacturers to access their software and data from anywhere, facilitating remote work and global operations. Cloud-based manufacturing software offers significant flexibility in terms of scalability and cost-efficiency. Companies can easily scale their software usage up or down based on their needs, without having to invest heavily in new hardware or infrastructure. This is particularly beneficial for manufacturers who experience seasonal fluctuations in demand or who need to accommodate multiple sites across different regions.
-
Collaboration and Integration: Cloud computing also enhances collaboration across teams and locations. By hosting manufacturing software on the cloud, companies can enable real-time collaboration among employees, regardless of their physical location. Teams can access and work on the same set of data simultaneously, leading to more efficient communication and decision-making. Cloud-based software also allows manufacturers to integrate their systems more easily with other enterprise applications, such as ERP and CRM systems, improving data flow and business operations.
-
Disaster Recovery and Security: Cloud platforms provide robust disaster recovery capabilities, ensuring data protection and continuity in case of system failures or data breaches. Cloud providers typically offer built-in security measures, such as encryption, multi-factor authentication, and regular backups, which are essential for protecting sensitive manufacturing data. This level of security reduces the risk of data loss and ensures compliance with industry standards.
Conclusion
Specialized manufacturing software is changing the industry by making processes more efficient, reducing costs, and helping with better decision-making. Choosing the right software and addressing any challenges during implementation can help manufacturers improve their operations and meet market demands. Companies that develop manufacturing software are key to this progress. For manufacturers wanting to stay competitive in a fast-changing world, investing in this technology is essential.