Nitroethane Manufacturing Plant Project Report 2025: Process, Cost and Consideration
Explore the comprehensive Nitroethane Manufacturing Plant Project report, covering production processes, safety standards, market trends, and financial projections.
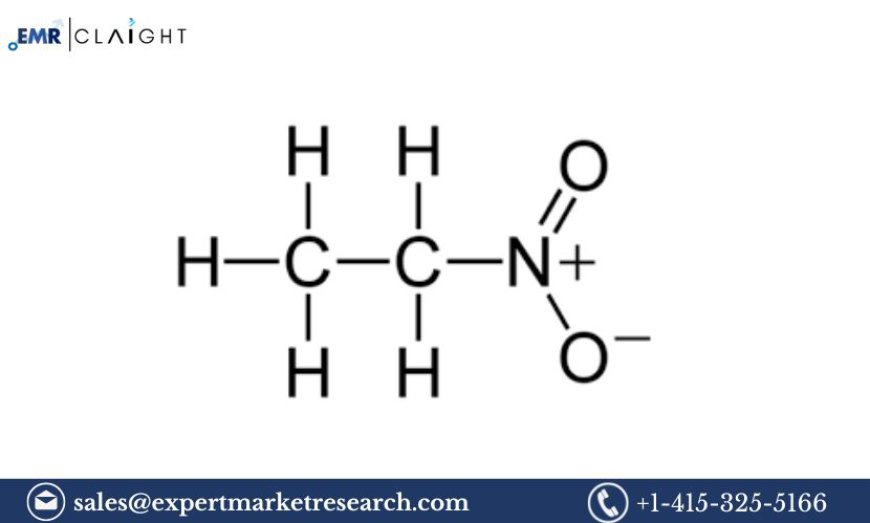
Introduction
A Nitroethane Manufacturing Plant Project Report provides an in-depth guide for establishing a facility dedicated to the production of nitroethane, a valuable organic compound used in various industrial and chemical applications. Nitroethane (C2H5NO2) is an important intermediate in the synthesis of other chemicals, and it has diverse uses in fields such as pharmaceuticals, agriculture, fuel additives, and explosives. This report will guide potential investors and businesses through the entire process of setting up a nitroethane manufacturing plant, covering market trends, the production process, equipment requirements, safety regulations, and financial projections.
Market Overview
Nitroethane has a wide range of applications across different sectors, and its demand is expected to continue growing due to its chemical versatility. The global market for nitroethane is influenced by its use as an intermediate for producing other chemicals, such as pharmaceuticals, agrochemicals, and explosives. Additionally, nitroethane’s use in fuel additives, which enhance the performance of gasoline and other fuels, contributes to the growing demand in the automotive and energy industries.
Key Market Drivers:
- Pharmaceutical Industry: Nitroethane is used in the pharmaceutical industry as a precursor for the synthesis of drugs and as an agent in drug formulations.
- Explosives and Fuel Additives: Nitroethane is employed in explosives production and as a fuel additive to enhance the performance of fuels in automotive and aerospace applications.
- Agriculture: Nitroethane is used in the manufacturing of agrochemicals and pesticides, which contribute to its steady demand in the agricultural sector.
- Chemical Manufacturing: As an organic solvent and reactant in various chemical reactions, nitroethane is used in the production of a variety of industrial chemicals.
Get a Free Sample Report with Table of Contents@
Manufacturing Process of Nitroethane
The production of nitroethane involves the nitration of ethane, which requires precise control of temperature and reagents. Below is an overview of the production process:
1. Raw Materials and Chemical Reactions
The key raw materials required for the production of nitroethane are ethane and nitric acid.
2. Production Process
The production of nitroethane generally follows these steps:
- Preparation of Reactants: The first step in the manufacturing process is to prepare the necessary reagents. Ethane is typically supplied in gaseous form, while concentrated nitric acid is used as the nitrating agent.
- Nitration Reaction: The ethane is mixed with nitric acid under controlled conditions, where the nitration reaction takes place. This is usually done in a reactor vessel where temperature and pressure are carefully regulated to ensure a smooth and controlled reaction. The temperature is typically maintained between 50°C and 100°C to optimize yield and minimize the formation of by-products.
- Separation and Purification: After the nitration reaction, the product mixture contains nitroethane along with other by-products. This mixture is then subjected to a separation process, usually involving distillation or solvent extraction, to isolate pure nitroethane from other substances.
- Drying: Nitroethane is hygroscopic and can absorb moisture, which could impact its purity and performance. Therefore, it is typically dried using anhydrous materials or other methods to ensure the final product is moisture-free.
- Storage and Packaging: Once purified and dried, the nitroethane is stored in sealed containers under appropriate conditions to prevent degradation. It is typically packaged in bulk containers or drums, depending on the application and distribution requirements.
3. Safety Measures in Production
Due to the highly reactive nature of nitric acid and the potentially hazardous chemicals involved in the production of nitroethane, the manufacturing process must be carried out under stringent safety measures:
- Explosion Prevention: The nitration reaction is exothermic, and care must be taken to control the temperature to prevent dangerous thermal runaway reactions. The plant should have explosion-proof equipment and systems to prevent accidental combustion.
- Ventilation: Adequate ventilation systems should be in place to manage fumes generated during the nitration process. The release of hazardous gases, such as nitrogen oxides, must be minimized through effective exhaust and filtration systems.
- Personal Protective Equipment (PPE): Workers involved in the production process should wear appropriate PPE, such as gloves, goggles, and protective clothing, to safeguard against exposure to hazardous chemicals.
- Fire Safety: Nitroethane is highly flammable, and special attention must be paid to fire prevention and suppression systems throughout the plant.
Equipment and Technology for Nitroethane Manufacturing
The production of nitroethane requires specialized equipment to handle the nitration reaction, separation, and purification processes. Some of the key equipment used in a nitroethane manufacturing plant includes:
- Nitration Reactors: These are designed to handle the reaction between ethane and nitric acid. They must be equipped with temperature and pressure control systems to manage the exothermic reaction safely.
- Distillation Columns: These are used to separate the nitroethane from the reaction mixture and purify it by removing impurities and by-products.
- Solvent Extraction Units: In some cases, solvent extraction may be used to isolate nitroethane from other components in the reaction mixture.
- Drying Units: These systems are used to remove moisture from the final product to ensure the purity and stability of nitroethane.
- Storage Tanks and Drums: For the safe storage and transportation of the final product, nitroethane is typically stored in high-quality, sealed tanks or drums designed to prevent leaks and contamination.
Financial Considerations
Setting up a nitroethane manufacturing plant involves significant investment, but with increasing demand in multiple industries, it can be a profitable venture. Key financial considerations include:
1. Initial Investment
- Land and Facility Setup: Costs for acquiring land, constructing the manufacturing facility, and setting up necessary utilities such as electricity, water, and waste management systems.
- Machinery and Equipment: Significant capital will be required for purchasing and installing specialized equipment like nitration reactors, distillation columns, and drying units.
- Licensing and Compliance Costs: Fees for obtaining necessary permits, complying with safety regulations, and ensuring environmental compliance.
2. Operational Costs
- Raw Materials: The cost of ethane and nitric acid, as well as solvents and other chemicals required for production.
- Labor: Wages for skilled workers, technicians, and safety personnel involved in the manufacturing process.
- Energy Consumption: The production process requires significant energy for heating, cooling, and operating machinery, which can add to operational costs.
- Maintenance: Ongoing costs to maintain and repair machinery and equipment.
3. Revenue Generation
- Sales of Nitroethane: The primary revenue will come from the sale of nitroethane to industries such as pharmaceuticals, chemicals, automotive, and agriculture.
- Pricing: The price of nitroethane is influenced by factors such as purity, market demand, and production scale.
FAQ
1. What is Nitroethane used for?
Nitroethane is used in pharmaceuticals, fuel additives, explosives, and agrochemicals. It serves as an intermediate for the synthesis of other chemicals.
2. Is Nitroethane flammable?
Yes, nitroethane is highly flammable and should be handled with extreme care. Proper safety measures, such as fire suppression systems and proper storage, are essential.
3. How is Nitroethane produced?
Nitroethane is primarily produced by nitrating ethane with nitric acid under controlled conditions. The reaction yields nitroethane and water as a by-product.
4. What safety precautions are necessary in Nitroethane manufacturing?
Safety measures include explosion-proof equipment, temperature and pressure control systems, fire safety protocols, and the proper handling and storage of hazardous chemicals.
5. What are the environmental concerns with Nitroethane production?
Nitroethane production can generate hazardous waste and emissions, requiring proper waste management and emissions control systems to minimize environmental impact.
Media Contact:
Company Name: Claight Corporation
Contact Person: Lewis Fernandas, Corporate Sales Specialist — U.S.A.
Email: sales@expertmarketresearch.com
Toll Free Number: +1–415–325–5166 | +44–702–402–5790
Address: 30 North Gould Street, Sheridan, WY 82801, USA
Website: www.expertmarketresearch.com
Aus Site: https://www.expertmarketresearch.com.au