Optical CMM Machine: Benefits, Challenges, and Future Trends
Coordinate Measuring Machines (CMM) has become one of the vital tools of manufacturing industries that provide dimensional control in manufacturing and measure the accuracy of the product.
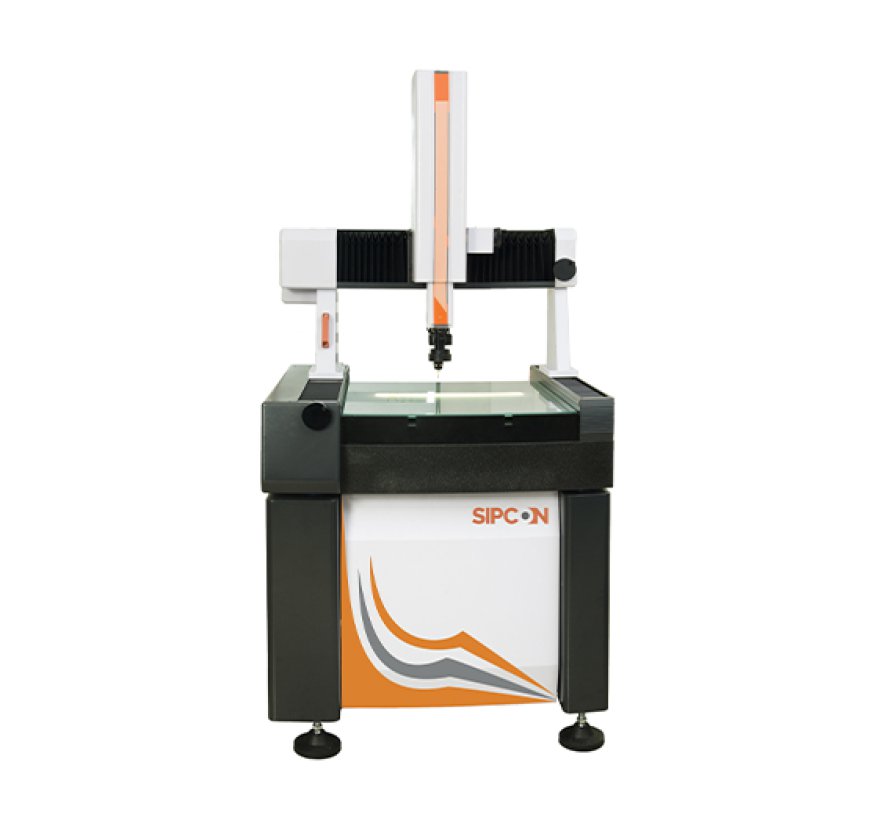
Coordinate Measuring Machines (CMM) has become one of the vital tools of manufacturing industries that provide dimensional control in manufacturing and measure the accuracy of the product. Optical probes are frequently used in CMM machines to feel or see the geometry of those objects that are to be measured.
Optical CMM machine of a higher level use probes that are not making contact with the object, instead using lasers or cameras to measure the object. These machines are used in applications where the difference between the sizes of an object is paramount in determining its application. In today’s production lines, where processes and tolerances become tighter and tighter, CMM and Optical CMM machines guarantee that those manufactured parts will conform to such very high accuracy.
Understanding the CMM Machines
A coordinate Measuring Machine (CMM) is a high-precision instrument by which the geometric dimensions of the object are determined at certain points on its surface. CMM machines operate with probes – through probes that physically touch and measure the part or through optics like laser or camera. These probes are used to obtain data for the determination of dimensions including length, width, and depth.
CMM machine in particular introduced the automated system of examining the quality of manufactured products with especial accuracy that is free from human interferences in allowing manufacturing companies to produce products with tight and dependable specifications.
Overview: Optical CMM Machines
An Optical CMM (Coordinate Measuring Machine) is an off-contact measuring solution that employs optical measuring techniques like lasers, cameras, or light-sensitive devices to obtain data points on a specific surface. As opposed to touch-based CMM machines where a probe contacts the object, Optical CMM machines measure contactless which allows for use for inspection of delicate, soft, or even complex geometries.
Optical CMM equipment uses methods like triangulation or interferometry in an effort to acquire the measures. Optical CMM is used extensively in aerospace, automobile, electronics, and manufacturing of medical instruments to control the quality and perform dimensional measurements. These machines are most advantageous in such areas of accuracy where contact devices may mar the product.
Challenges encountered in optical CMM measurement
Optical CMM machines produce even greater accuracies and reliability, but they also present problems that can influence the general performance. These challenges crop up because optical measurement systems are particularly sensitive.
· Sensitivity to environmental conditions: The systems used in optical CMM machines are sensitive to light, temperature, and humidity and these factors affect measurements.
· Calibration and alignment issues: Non-corrective alignment of the optical components is essential; any irregularity distorts the measurements obtained.
· Limitations in material measurement: Some of the challenges of optical sensors are that some materials like the transparent or the reflective ones will give a low precision while capturing the data.
Future Trends in CMM Technology
The application of CMM technology is developing very fast, and recent advancements are opening new possibilities for users, particularly in terms of precision measurement. Continued integration as well as new measurement systems are the future of the advance of CMM technology.
· Integration with digital technologies: AI and machine learning will also be used to enhance transparent real-time data collection to make CMM machines more intelligent.
· Innovations in optical measurement techniques: There are innovations in the optical sensor to resolve more details and faster in capturing intricate shapes.
· Impact on manufacturing processes: That should Progress in CMM machines means the reduction of control, which is usually done by human beings, thereby increasing efficiency when it comes to production.
Benefits of Optical CMM Machines
Various operating principles of Optical CMM equipment make them suitable for many sectors due to offering accurate, contactless measurements. Characterized by their potential to deliver high-detail data with the least interferences to the measured object, there are several antecedent merits associated with resonant frequency measurements. The following are some benefits associated with this CMM machine:
· Non-contact measurement: Optical CMMs are capable of measuring characteristics on delicate or flexible material without having to touch the said material thus avoiding the alteration of the material.
· High-speed data capture: Optical systems are ideal for taking complex geometries and can therefore save time in cases where the operation is time-sensitive.
· Enhanced accuracy: These machines are ideal for fine feature measurements, especially for complex designs of parts.
· Adaptability to different environments: The use of the latest optical engineering makes these machines flexible in terms of lighting regression rates and different surface finishes making them more versatile across uses.
Conclusion
Industries use both the Optical CMM machines and the customary CMM machines relevant to manufacturing and quality assurance. Many of them offer accurate measuring parameters that improve effectiveness, productivity, and creativity across all sectors and allow businesses to maintain superior quality and manage growing levels of production challenges.