Techniques to Achieve Reliable Melt Flow Index Testing Results Every Time
The melt flow index tester, also called an MFI tester, is an instrument used to determine the flow rate of thermoplastic polymers in grams per ten minutes.
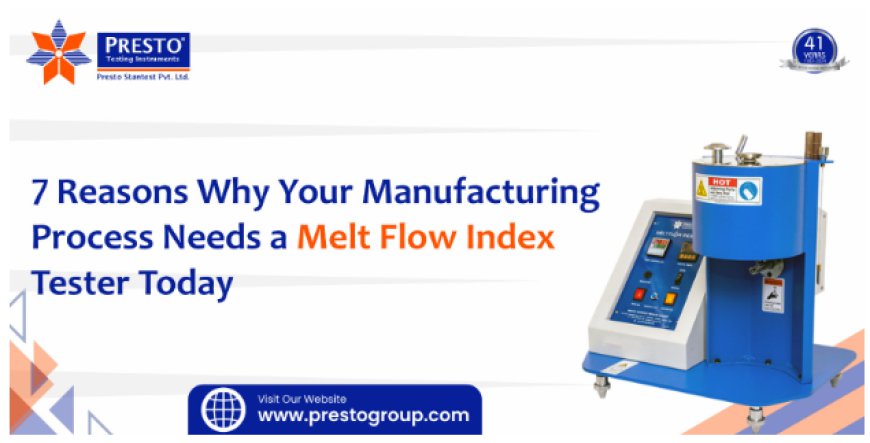
The melt flow index tester, also called an MFI tester, is an instrument used to determine the flow rate of thermoplastic polymers in grams per ten minutes. This measurement is taken under controlled temperature and pressure, giving manufacturers insight into the viscosity of the plastic when it’s in a molten state. Different materials have unique MFI values, and understanding these values is essential for selecting the right plastic for a particular application, from packaging and construction to automotive and consumer goods.
How Does a Plastic Melt Flow Index Tester Work?
The plastic melt flow index tester operates based on a straightforward yet highly precise process. Here’s a brief rundown of how it works:
Sample Preparation: A small sample of the plastic material is prepared and loaded into the machine's barrel, which is preheated to a specific temperature based on the material type.
Application of Force: The material is heated until it reaches a molten state. Then, a specified weight or force is applied to push the molten material through a narrow capillary die at the bottom of the barrel.
Measurement of Flow: As the molten plastic exits the capillary, the device measures the amount of material that flows through over a specified period, usually ten minutes.
Calculation of MFI: The melt flow index tester then calculates the MFI by dividing the weight of the material extruded by the time, giving a result in grams per ten minutes.
The plastic melt flow index tester provides data critical to quality assurance, as it indicates how a plastic material will behave in various applications. For instance, a high MFI value suggests the material flows easily, which may be ideal for injection molding but less suitable for structural applications requiring high strength.
Key Benefits of Using a Melt Flow Index Tester
Using a melt flow index tester offers several benefits, especially in quality control and manufacturing. Here are some key advantages:
Quality Control: The melt flow index is a standard measurement that helps ensure that every batch of plastic meets the required specifications, reducing variability and maintaining product quality.
Material Selection: By knowing the MFI, manufacturers can choose the right material for each application. For instance, high-flow plastics are often used in applications that require quick mold filling, whereas low-flow plastics are chosen for structural applications.
Cost Efficiency: The ability to detect issues in material consistency early helps manufacturers avoid costly errors, reworks, and waste.
Process Optimization: Knowing the melt flow properties allows manufacturers to adjust processing parameters for different materials, optimizing production time and minimizing downtime.
Regulatory Compliance: Many industries have stringent quality and safety standards. Using a plastic melt flow index tester helps ensure compliance with these standards, reducing the risk of product recalls.
Types of Melt Flow Index Testers
When looking for a melt flow index tester manufacturer, it’s essential to understand the types of MFI testers available on the market. While the fundamental principle of operation remains the same, different testers may offer various features and levels of automation.
Manual MFI Testers: These testers require operators to manually record and calculate the MFI. They are generally less expensive and suitable for smaller labs or companies with lower testing volumes.
Semi-Automated MFI Testers: These testers automate some aspects of the testing process, such as cutting off the extruded material and timing, making the process more efficient.
Fully Automated MFI Testers: These high-end testers handle all aspects of the testing process automatically, from sample extrusion to measurement and calculation. They are ideal for high-throughput labs that perform frequent MFI testing.
Each type has its own advantages, and the choice depends on factors like budget, required precision, and testing frequency. A reputable melt flow index tester manufacturer will offer a range of options to meet different operational needs.
Selecting the Right Melt Flow Index Tester Manufacturer
When investing in a melt flow index tester, choosing the right manufacturer is crucial for ensuring durability, accuracy, and support. Here are some factors to consider when selecting a melt flow index tester manufacturer:
Quality and Durability: Look for a manufacturer with a reputation for producing reliable and durable equipment. The tester should be made from high-quality materials and withstand constant use without significant wear.
Accuracy and Precision: Precision is essential in melt flow testing. Check for certifications and accuracy specifications to ensure the tester meets industry standards.
Customer Support and Training: A good manufacturer will provide customer support and training to ensure users can operate the equipment effectively and address any issues that arise.
Calibration and Maintenance Services: Regular calibration and maintenance are vital for ensuring consistent accuracy. Opt for manufacturers who offer these services or have partnerships with service providers.
Advanced Features: Some testers come with digital interfaces, data logging, and connectivity features that streamline the testing process and make it easier to store and analyze data.
By choosing a trusted melt flow index tester manufacturer, companies can gain confidence in their testing results and maintain high standards in plastic production.
Applications of Melt Flow Index Testers in Different Industries
The melt flow index tester is used across various industries, each with unique applications:
Packaging: Packaging materials require specific flow properties for molding processes, and MFI testing helps ensure these properties are met.
Automotive: Automotive components often need durable plastics with low MFI to enhance structural integrity.
Consumer Goods: MFI testing helps select plastics with the right flow characteristics for everyday items, ensuring consistency and quality.
Medical: Medical equipment and packaging rely on precise MFI values to ensure reliability, safety, and regulatory compliance.
Conclusion
A melt flow index tester is essential for plastic manufacturers to control quality, optimize production, and select appropriate materials. Whether you’re a small business or a large enterprise, the right plastic melt flow index tester will help you produce consistent and high-quality plastic products. Selecting a reliable melt flow index tester manufacturer is equally important, as it ensures your equipment will provide accurate results over time.
For more information on melt flow index testers or to inquire about specific models, contact a reputable manufacturer for guidance.