The Essential Guide to Drop-In Anchors, Anchor Bolts, Rental Stud Welding Machines, and Self-Drilling Screws
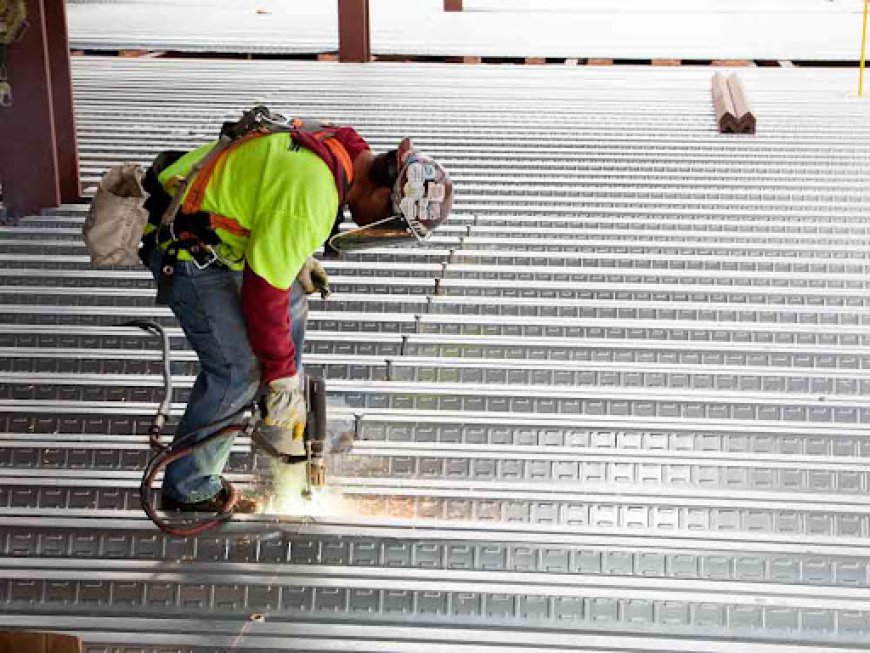
In the field of construction and structural engineering, reliable fastening solutions are crucial for ensuring the stability and safety of structures. From securing steel beams to anchoring heavy machinery, various types of fasteners play a key role in connecting structural elements. Among these, drop-in anchors, anchor bolts, stud welding machines, and self-drilling screws are indispensable tools that help achieve strong, lasting connections. This guide delves into each of these components, exploring their uses, installation processes, and benefits.
1. Drop-In Anchors: Reliable Fastening for Concrete Applications
Drop-in anchors are specialized fasteners used to anchor threaded rods, bolts, or other hardware into concrete surfaces. They are internally threaded anchors designed to provide a strong, reliable hold in solid concrete, making them an excellent choice for heavy-duty applications.
a. What Are Drop-In Anchors?
A drop-in anchor is a cylindrical, expansion-type anchor made of steel. It features an internal threading and a hollow body that expands when a setting tool is used. This expansion creates a secure grip within the concrete, allowing for high load capacities.Pull Out Testing
b. Common Applications of Drop-In Anchors
Securing Suspended Ceilings: Drop-in anchors are commonly used to install ceiling hangers for suspended ceilings and electrical fixtures.
Anchoring Heavy Machinery: In industrial settings, they are used to fasten heavy equipment to concrete floors.
Structural Steel Connections: Drop-in anchors are ideal for attaching steel beams, columns, and brackets to concrete structures.
c. Installation Process
Installing drop-in anchors is straightforward but requires proper tools and techniques to ensure maximum strength:
Drill a Hole: Use a hammer drill to create a hole in the concrete, matching the diameter of the drop-in anchor.
Clean the Hole: Remove any dust or debris using a brush or air blower, as this ensures proper expansion of the anchor.
Insert the Anchor: Place the drop-in anchor into the drilled hole, with the open end facing outward.
Set the Anchor: Use a setting tool to expand the anchor. This tool is inserted into the anchor and struck with a hammer, causing the anchor body to expand and grip the concrete.
Attach the Fastener: Once the anchor is set, a threaded rod or bolt can be inserted and tightened.
2. Anchor Bolts: Versatile Fastening for Structural Stability
Anchor bolts are heavy-duty fasteners used to attach structural elements to concrete. They are essential for transferring loads from the structure to the foundation, providing stability and preventing movement.
a. Types of Anchor Bolts
Cast-in-Place Anchor Bolts: These bolts are installed during the concrete pouring process. The bolts are embedded directly into the wet concrete and allowed to set, providing a strong, permanent hold.
Expansion Anchor Bolts: Similar to drop-in anchors, these bolts use expansion sleeves that grip the sides of a pre-drilled hole in hardened concrete.
Epoxy Anchor Bolts: These bolts are installed using a special adhesive (epoxy resin) that bonds the bolt to the concrete surface.
b. Key Applications of Anchor Bolts
Securing Steel Columns: Anchor bolts are used to fasten steel columns to concrete foundations, ensuring the structural integrity of buildings and bridges.
Attaching Machinery: In industrial facilities, anchor bolts secure heavy machinery and equipment to prevent shifting during operation.
Wind Turbines and Poles: Tall structures like wind turbines and utility poles rely on anchor bolts to withstand wind and seismic forces.
c. Installation Tips
Proper Drilling: Ensure the hole depth matches the length of the anchor bolt for a secure fit.
Use of Adhesives: For epoxy anchor bolts, follow the manufacturer’s guidelines for adhesive application to achieve maximum bonding strength.
Torque Application: Tighten the bolts to the specified torque to avoid over-stressing the fastener or concrete.
3. Rental Stud Welding Machines: A Cost-Effective Solution for High-Volume Projects
Stud welding is a fast, efficient method for attaching metal studs to a base material, typically used in construction, shipbuilding, and automotive industries. Renting a stud welding machine is a practical choice for contractors and builders who need this equipment for a specific project but want to avoid the high upfront cost of purchasing.
a. Benefits of Renting Stud Welding Machines
Cost Savings: Renting eliminates the need for a large investment, reducing costs for short-term projects.
Access to Advanced Technology: Rental options often include the latest models with advanced features, enhancing efficiency and precision.
Maintenance-Free: Rental machines are typically maintained by the rental company, ensuring they are in top working condition.
b. Types of Stud Welding Machines
Drawn Arc Stud Welding Machines: Used for heavy-duty applications, these machines create strong welds for large-diameter studs.
Capacitor Discharge (CD) Stud Welding Machines: Suitable for smaller studs and thinner materials, these machines offer a fast, low-heat process that minimizes distortion.
c. How to Use a Stud Welding Machine
Prepare the Surface: Clean the base material to remove any rust, paint, or contaminants.
Load the Stud: Insert the stud into the welding gun.
Position the Stud: Place the welding gun against the base material.
Activate the Weld: Trigger the welding gun to create an arc, melting the base of the stud and fusing it to the surface.
Inspect the Weld: Check the weld for strength and quality, ensuring a secure connection.
4. Self-Drilling Screws: The Ultimate Fastener for Speed and Efficiency
Self-drilling screws are versatile fasteners designed to drill their own hole and tap their own thread as they are driven into materials. These screws eliminate the need for pre-drilling, saving time and labor on job sites.
a. Features of Self-Drilling Screws
Built-In Drill Tip: The tip of the screw functions as a drill bit, allowing it to penetrate materials such as metal, wood, and plastic.
Threading for Secure Hold: The threads cut into the material as the screw is driven, creating a tight, vibration-resistant connection.
Variety of Coatings: Self-drilling screws often come with coatings (e.g., zinc, galvanized) to resist corrosion, making them suitable for outdoor use.
b. Common Uses of Self-Drilling Screws
Metal Roofing: Self-drilling screws are widely used in metal roofing projects, as they easily penetrate steel sheets and provide a waterproof seal.
Steel Framing: In steel construction, these screws are used to fasten metal studs and beams without the need for additional tools.
HVAC and Electrical Installations: Self-drilling screws simplify the process of securing ducts, conduit, and electrical components.
c. Best Practices for Using Self-Drilling Screws
Choose the Right Screw Size: The screw size should be appropriate for the thickness of the material to ensure proper penetration and holding strength. Rental Stud Welding Machine
Use a Power Drill: A power drill with adjustable torque settings helps drive the screws quickly and efficiently without damaging the material.
Apply Consistent Pressure: Avoid excessive force, as this can strip the threads and compromise the connection.
Conclusion
Drop-in anchors, anchor bolts, rental stud welding machines, and self-drilling screws are essential tools and fasteners in construction and industrial applications. Each of these components plays a unique role in creating strong, reliable connections that contribute to the safety and durability of structures. Understanding their uses, installation processes, and benefits can help contractors, builders, and engineers choose the right solutions for their projects.
By leveraging the right tools and techniques, construction professionals can enhance efficiency, reduce costs, and ensure the successful completion of even the most challenging projects. Whether you are securing steel columns, installing roofing panels, or welding studs, these fastening solutions provide the reliability and performance needed to meet industry standards and exceed client expectations.