The Evolution of Lathe Chuck Manufacturing: From Early Designs to Modern Precision Technology
Discover the fascinating history of lathe chuck manufacturing, from its humble beginnings in the 18th century to the advanced technology used today. Learn how innovations like 3-jaw and 4-jaw chucks, hydraulic systems, and CNC automation have revolutionized machining processes, ensuring greater precision and efficiency. Explore the future of lathe chuck technology and its impact on modern industries.
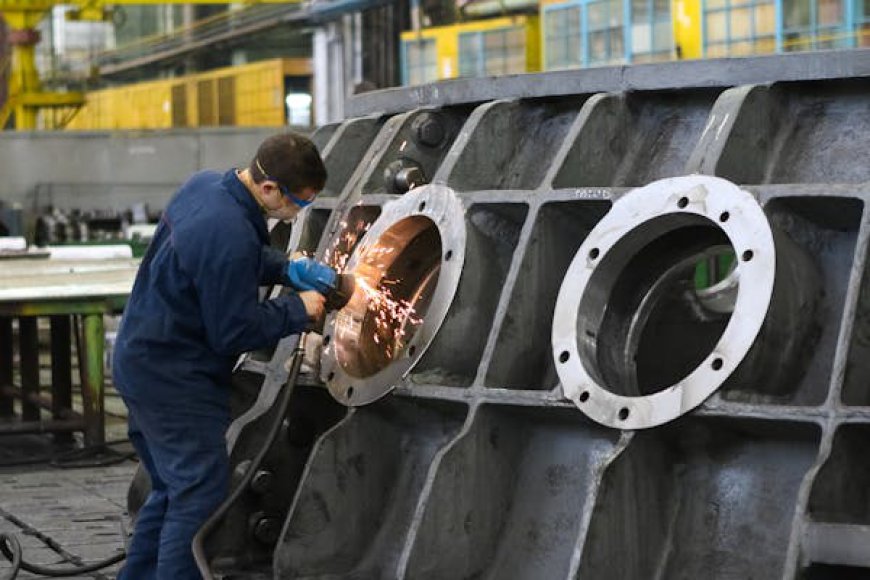
The lathe chuck is an essential tool in metalworking, woodworking, and many other industries. It securely holds the workpiece, allowing for precision in shaping, drilling, or machining. Over the years, lathe chuck technology has evolved significantly, improving both efficiency and accuracy in manufacturing processes. In this blog, we’ll explore the history of lathe chuck manufacturing and how the technology has developed over time.
1. Early Beginnings: The Birth of the Lathe Chuck
The history of lathe chucks dates back to the late 18th century, during the Industrial Revolution. As factories began to produce more complex machines, there was a growing need for tools that could hold workpieces securely in place. Early lathe chucks were simple, relying on manual tightening mechanisms.
-
Wooden Chucks: In the early days, lathe chucks were made of wood and used mainly for woodworking. These wooden chucks had limited precision and durability, but they laid the groundwork for future advancements.
-
Basic 2-Jaw Chucks: Early metal lathes used 2-jaw chucks, which were manually adjusted. While not as versatile as modern chucks, these were a breakthrough in holding irregularly shaped workpieces.
2. The Introduction of 3-Jaw and 4-Jaw Chucks
The 19th century saw significant improvements in chuck design with the introduction of more advanced types:
-
3-Jaw Chucks: Invented in the mid-1800s, 3-jaw chucks became the standard for holding cylindrical workpieces. Their self-centering feature made them popular for many applications, as they could automatically center the workpiece for more accurate machining.
-
4-Jaw Chucks: The development of 4-jaw chucks provided greater flexibility, allowing workers to clamp irregular shapes. These independent jaws could be adjusted separately, which made it easier to hold non-round workpieces.
3. The Rise of Mass Production and Precision Engineering
In the early 20th century, lathe chuck manufacturing saw another wave of innovation, driven by advancements in mass production and precision engineering.
-
Improved Materials: The introduction of stronger metals, such as hardened steel, made chucks more durable and long-lasting. This also improved the accuracy of the chuck’s grip, as wear and tear were reduced.
-
Scroll and Spiral Mechanisms: The invention of scroll and spiral mechanisms for adjusting chuck jaws made it easier to hold various workpiece sizes without manual readjustment. This development greatly improved efficiency in machine shops.
-
Standardization: As manufacturing grew, the need for standard-sized chucks became apparent. Standardization made it easier for manufacturers to produce compatible parts, leading to more consistent and reliable machining processes.
4. Post-World War II Innovations
After World War II, lathe chuck technology advanced even further as industrial demand for precision grew. During this time, key innovations included:
-
Hydraulic and Pneumatic Chucks: These automated chucks reduced the need for manual adjustment, increasing the speed and efficiency of production lines. Hydraulic and pneumatic chucks were particularly useful in high-volume manufacturing.
-
Quick-Change Chucks: Quick-change technology made it possible to swap out chuck jaws faster, reducing downtime and increasing productivity. This feature became essential in industries where time efficiency was crucial, such as automotive manufacturing.
5. Modern Lathe Chuck Manufacturing
Today, lathe chuck technology has reached new heights, with manufacturers focusing on precision, efficiency, and versatility.
-
CNC Chucks: With the rise of computer numerical control (CNC) machines, lathe chucks have become more advanced, offering precise control over positioning and gripping force. CNC chucks are now a cornerstone of modern automated manufacturing.
-
Custom and Specialized Chucks: Manufacturers now produce custom chucks designed for specific industries, such as aerospace or medical device manufacturing. These specialized chucks are made to meet precise specifications, ensuring high-quality results in highly regulated industries.
-
Eco-Friendly Manufacturing: In recent years, manufacturers have focused on reducing the environmental impact of chuck production. This includes using more sustainable materials and energy-efficient manufacturing processes.
6. The Future of Lathe Chuck Technology
As technology continues to advance, the future of lathe chuck manufacturing will likely see even greater innovations:
-
Smart Chucks: With the rise of Industry 4.0, “smart” chucks equipped with sensors and real-time monitoring capabilities could become a reality. These chucks would offer feedback on performance, wear, and alignment, ensuring optimal machining conditions at all times.
-
Advanced Materials: Future chucks may be made from even stronger and lighter materials, such as composites or alloys, improving durability and performance.
-
Automation and AI Integration: Automation and artificial intelligence will play a larger role in chuck manufacturing, streamlining processes and further reducing human error.
Conclusion
The history of lathe chuck manufacturing is one of continuous innovation and improvement. From the early wooden chucks of the 18th century to today’s high-tech CNC and hydraulic models, lathe chucks have come a long way. As we look to the future, it's clear that lathe chuck technology will continue to evolve, driving precision and efficiency in the manufacturing world.