Understanding PP Fibrillated Yarn: Characteristics, Production, and Applications
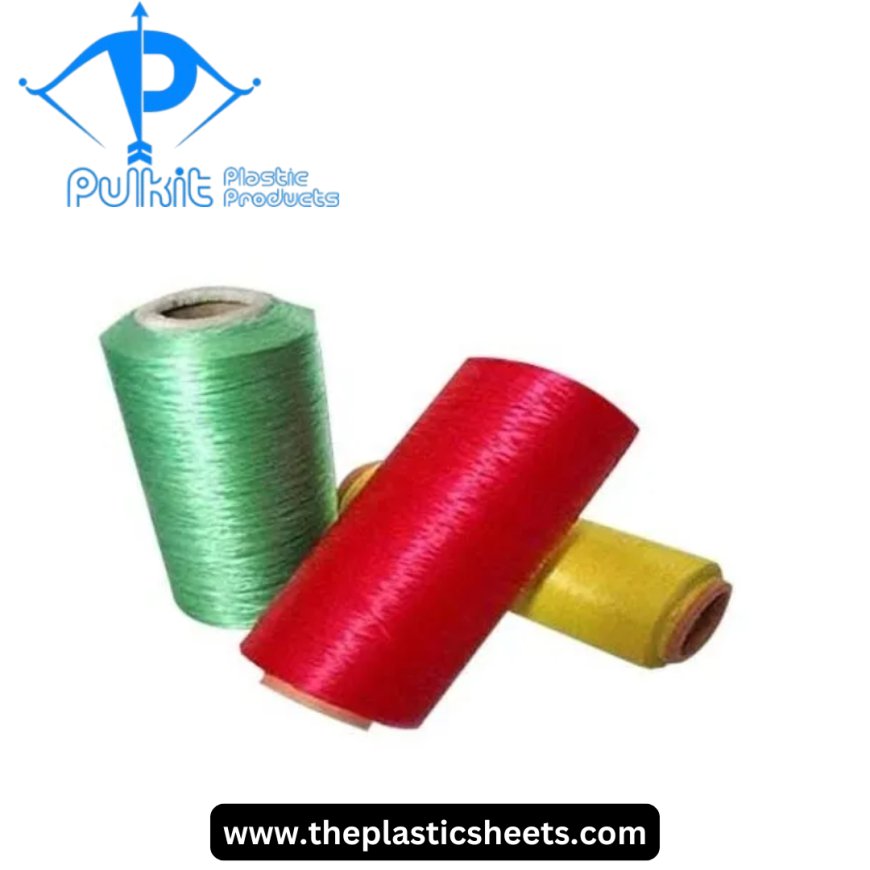
PP fibrillated yarn, a specialized form of polypropylene filament yarn, has garnered attention in various industries due to its unique properties and versatile applications. Fibrillation refers to the process of splitting or fibrillating the fibers of the yarn into finer strands, resulting in a distinctive texture that enhances the yarn's usability. Produced primarily from polypropylene, this type of yarn is lightweight, durable, and offers excellent resistance to moisture, UV rays, and chemicals. This Pulkit Plastic Products explores the characteristics, production processes, applications, and market landscape of PP fibrillated yarn, with a particular focus on the role of polypropylene yarn manufacturers in India.
Characteristics of PP Fibrillated Yarn
When it comes to understanding the significance of polypropylene filament yarn, it is essential to highlight the attributes that make PP fibrillated yarn stand out. The fibrillation process significantly increases the surface area of the yarn, resulting in greater flexibility and softness. This allows for enhanced bonding characteristics, making it ideal for use in composite materials, textiles, and geotextiles.
Moreover, PP fibrillated yarn exhibits exceptional tensile strength and elongation, enabling it to withstand harsh environmental conditions. These properties make it suitable for demanding applications such as industrial fabrics, agricultural covers, and packaging materials. Additionally, the yarn's hydrophobic nature means it does not absorb water, combating issues like mold and mildew while remaining lightweight even in wet conditions.
Another notable characteristic of PP fibrillated yarn is its resistance to chemicals and UV rays. It does not degrade or lose color when exposed to harsh chemicals, making it suitable for outdoor applications. These factors combined make PP fibrillated yarn an excellent choice for industries requiring reliable, long-lasting materials.
The Production Process of PP Fibrillated Yarn
The production of Polypropylene fibrillated yarn involves several critical steps. The process begins with the extrusion of molten polypropylene through a spinneret, where it solidifies into continuous filaments. The fibrillation process occurs during the mechanical treatment, wherein the yarn is stretched and manipulated to create multiple smaller strands from the main fibers.
Once the yawn has been fibrillated, it undergoes additional treatments to enhance its properties. This may include applying UV stabilizers to extend the yarn's lifespan when used outdoors. Some manufacturers also add colorants or additives to improve specific aspects of the yarn's performance, such as stain resistance or fire retardancy, depending on the intended application.
Quality control plays a vital role throughout the production process. Manufacturers conduct rigorous testing to ensure the yarn meets various specifications, including tensile strength, elongation, and resistance to environmental factors. Such measures help to guarantee a high standard of quality in the yarn produced by polypropylene yarn manufacturers and ensure it can perform effectively across its intended applications.
Applications in Various Industries
PP fibrillated yarn finds its applications in a multitude of industries, thanks to its unique properties and versatility. In the agricultural sector, it is commonly used for applications such as shade cloth, mulch films, and crop covers. The increased surface area from fibrillation helps with better plant growth by facilitating light diffusion and minimizing heat stress on crops.
In the packaging industry, PP fibrillated yarn is often utilized in the production of woven bags and sacks that require strength and durability. These products benefit from the yarn's fibrous structure, which can provide additional load-bearing capacity. The breathable nature of the yarn also helps prevent moisture buildup, preserving the integrity of the products stored inside.
Furthermore, PP fibrillated yarn is making significant headway in the automotive industry, where it is used in applications such as upholstery and interior linings. The lightweight yet strong nature of the yarn contributes to fuel efficiency in vehicles, making it an attractive option for manufacturers looking to optimize performance. The yarn's resistance to chemicals, UV rays, and moisture further enhances its suitability for automotive applications.
The Role of Polypropylene Yarn Manufacturers in India
India has emerged as a hub for polypropylene yarn production, with numerous polypropylene yarn manufacturers operating within its borders. The presence of advanced manufacturing facilities, skilled labor, and an increasing demand for products made from polypropylene has facilitated significant growth in this sector. Indian manufacturers often leverage cost-effective production processes while adhering to international quality standards, enabling them to compete effectively in the global market.
Moreover, the rise of sustainability consciousness among consumers has led to increased interest in eco-friendly practices among manufacturers. Many Indian companies are now investing in recycling initiatives and sustainable production methods to minimize their environmental impact. This trend aligns with the global shift towards sustainability, positioning Indian manufacturers favorably for future growth.
As the demand for PP fibrillated yarn continues to rise across multiple sectors, Indian manufacturers are increasingly expanding their product portfolios and exploring innovative applications. By engaging in research and development, these companies strive to enhance the attributes of their yarn offerings, ensuring they remain competitive and responsive to market changes.
Market Dynamics and Growth Potential
The global market for Polypropylene yarn manufacturers is projected to witness steady growth, driven by factors such as increasing demand from various industries, advancements in production technologies, and the rising focus on sustainable practices. The agricultural, packaging, and automotive sectors are expected to be significant contributors to this growth, as manufacturers recognize the advantages of utilizing fibrillated yarn in their products.
Additionally, the market is benefiting from the increasing popularity of nonwoven fabrics, which often incorporate PP fibrillated yarn into their manufacturing processes. As consumers look for lightweight, durable, and eco-friendly options, the adaptability and functionality that fibrillated yarn offers make it a preferred choice for manufacturers.
Furthermore, the continuous evolution of technology in production processes enhances the feasibility of different applications, expanding the potential for PP fibrillated yarn use. With innovations in fiber spinning, coating, and additives, manufacturers are finding new and exciting applications for this versatile material. As a result, businesses that invest in research and development to explore these opportunities are more likely to achieve a competitive edge in the market.
Sustainability Initiatives in the PP Yarn Industry
Sustainability has become a critical concern for industries worldwide, and the production of polypropylene filament yarn is no exception. Manufacturers are increasingly focusing on sustainable practices by adopting eco-friendly raw materials, minimizing waste, and optimizing energy consumption. In the case of PP fibrillated yarn, many companies are exploring ways to incorporate recycled polypropylene into their manufacturing processes, promoting a circular economy.
Moreover, various polypropylene yarn manufacturers are implementing waste management and recycling initiatives to minimize environmental impact. By recovering and repurposing materials, they contribute to resource conservation while maintaining efficiency in production. Many companies are establishing partnerships with environmental organizations and participating in sustainability programs to further enhance their credentials.
As consumer preferences evolve towards sustainability, manufacturers who emphasize environmentally responsible practices will likely gain a competitive advantage in the growing market. By prioritizing eco-friendly practices and materials, they can better align with the values of consumers and businesses seeking sustainable alternatives in their supply chains.
Conclusion
In conclusion, Polypropylene yarn manufacturers in india represents a significant advancement in the realm of polypropylene filament yarns, providing robust, lightweight, and versatile materials for various applications across multiple industries. Its unique production process and characteristics make it highly sought after within agriculture, packaging, and automotive sectors, while the growing prominence of sustainable practices in manufacturing illustrates its potential for continued growth.
As the demand for innovative and eco-friendly materials continues to rise, polypropylene yarn manufacturers, particularly in India, are well-positioned to capitalize on these opportunities. By focusing on technology advancements, sustainable practices, and creative applications, they can ensure the continued relevance of PP fibrillated yarn in the global market.
Frequently Asked Questions
Q1: What is PP fibrillated yarn and how is it different from regular polypropylene filament yarn?
A: PP fibrillated yarn is a type of polypropylene filament yarn that has undergone a fibrillation process, which splits the fibers into finer strands, enhancing flexibility and surface area. This makes it more suitable for various applications compared to regular filament yarn.
Q2: What are the primary applications of PP fibrillated yarn?
A: PP fibrillated yarn is widely utilized in agriculture for crop covers, in the packaging industry for woven sacks and bags, and in the automotive sector for upholstery and interior linings due to its strength, durability, and moisture resistance.
Q3: How do polypropylene yarn manufacturers in India contribute to the market?
A: Polypropylene yarn manufacturers in India play a crucial role in the global market by offering cost-effective products while adhering to international quality standards. They are increasingly adopting sustainable practices and focusing on innovative applications of fibers to stay competitive.