Why Hydroforming Technology is Essential in Lightweight Metal Fabrication
Sustainability is a growing concern in manufacturing, and hydroforming technology plays a vital role in addressing this challenge.
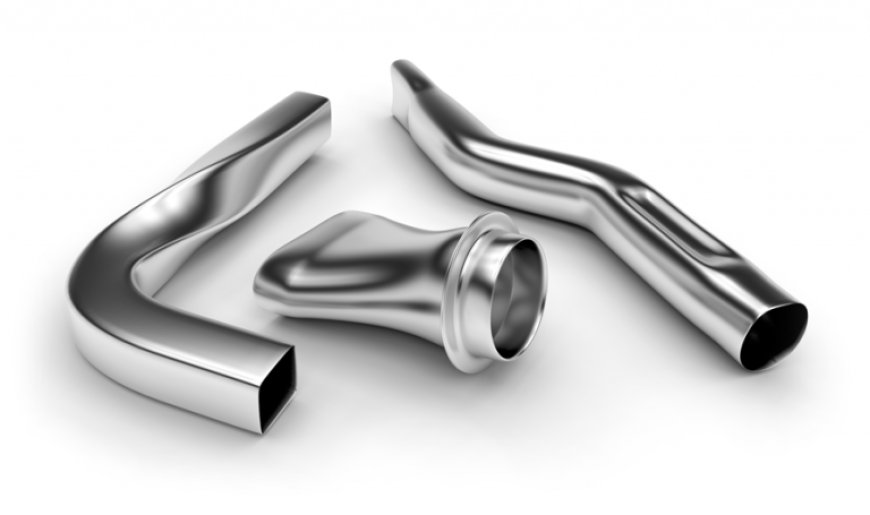
Hydroforming technology has revolutionized the manufacturing industry by enabling the production of lightweight, strong, and intricate metal components. This process, which uses fluid pressure to shape metal into complex geometries, is particularly advantageous in industries requiring high performance and weight reduction, such as automotive, aerospace, and consumer electronics. This article explores the significance of hydroforming technology in lightweight metal fabrication, delving into its benefits, applications, and future potential.
Understanding Hydroforming Technology in Metal Fabrication
Hydroforming technology involves using high-pressure fluids to shape metal sheets or tubes into desired forms. The process eliminates the need for traditional welding or assembly of multiple components, enabling manufacturers to produce seamless and intricate shapes. By applying pressure uniformly, hydroforming ensures that the metal's structural integrity is maintained, resulting in lightweight yet durable parts. This characteristic is critical in industries focused on performance and efficiency.
The process is versatile, allowing the fabrication of parts with complex geometries that would be challenging to achieve through conventional methods. Hydroforming enables manufacturers to work with a variety of materials, including aluminum, stainless steel, and titanium, which are commonly used in lightweight applications. This flexibility makes hydroforming an essential technology for modern metal fabrication.
Advantages of Hydroforming in Lightweight Applications
Hydroforming technology offers several advantages that make it ideal for lightweight metal fabrication. First, it allows for significant weight reduction without compromising the strength or durability of the components. This is particularly beneficial in the automotive and aerospace industries, where reducing weight translates to improved fuel efficiency and performance. Additionally, the process minimizes material wastage, as it uses precise amounts of metal to create parts, enhancing sustainability.
Another key advantage is the cost-effectiveness of hydroforming. By eliminating the need for welding and reducing material usage, manufacturers can achieve substantial cost savings. The seamless nature of hydroformed parts also reduces the risk of failure points, resulting in higher reliability and longer product lifespans. This combination of efficiency, durability, and cost savings underscores the importance of hydroforming in lightweight metal fabrication.
Applications of Hydroforming Technology in Lightweight Industries
Hydroforming technology is widely used in industries that prioritize lightweight materials and complex designs. In the automotive sector, for instance, hydroformed components are used to create lightweight chassis and frame structures that enhance vehicle performance and safety. By enabling intricate designs, hydroforming also supports the integration of features such as crumple zones, which improve crashworthiness.
In aerospace, hydroforming technology is crucial for fabricating lightweight yet robust components like wing spars, fuselage panels, and engine parts. The ability to produce precise, complex geometries ensures that aerospace manufacturers can meet stringent performance and safety standards. Similarly, in consumer electronics, hydroforming is used to create sleek, lightweight casings that enhance product aesthetics and usability.
The Role of Hydroforming in Sustainable Manufacturing
Sustainability is a growing concern in manufacturing, and hydroforming technology plays a vital role in addressing this challenge. By optimizing material usage and reducing waste, hydroforming contributes to more sustainable production processes. This is particularly important when working with expensive and energy-intensive materials like titanium and aluminum, where minimizing waste has both economic and environmental benefits.
Furthermore, hydroforming technology reduces the energy consumption associated with traditional metal fabrication techniques. The process eliminates the need for multiple machining steps, lowering the overall energy footprint of production. By supporting the creation of lightweight components, hydroforming also indirectly reduces emissions in applications like automotive and aerospace, where lighter parts lead to more fuel-efficient vehicles and aircraft.
Future Potential of Hydroforming Technology in Metal Fabrication
The future of hydroforming technology in lightweight metal fabrication is bright, driven by advancements in materials science and automation. Innovations such as high-strength alloys and composite materials are expanding the possibilities of hydroforming, enabling the production of even lighter and stronger components. Additionally, the integration of robotics and artificial intelligence is enhancing the precision and efficiency of the hydroforming process.
As industries continue to prioritize weight reduction and sustainability, the demand for hydroforming technology is expected to grow. From electric vehicles to next-generation aircraft, hydroforming will play a critical role in shaping the future of lightweight manufacturing. By combining efficiency, precision, and environmental benefits, hydroforming technology remains an indispensable tool in the quest for innovation and excellence in metal fabrication.
Conclusion
Hydroforming technology is a cornerstone of modern lightweight metal fabrication, offering unparalleled advantages in terms of efficiency, sustainability, and design flexibility. Its ability to create complex, durable, and lightweight components makes it indispensable in industries such as automotive, aerospace, and electronics. As advancements in materials and automation continue to evolve, hydroforming will remain at the forefront of innovation, driving the future of manufacturing.